Solder
Soldering is the art and science of joining electronic components using a specialized alloy to create reliable connections on Printed Circuit Boards (PCBs).There are several types of solder used in Printed Circuit Board Assembly (PCBA), each with its own characteristics and applications. The choice of solder type depends on factors such as assembly process, component type, reliability requirements, and regulatory compliance.
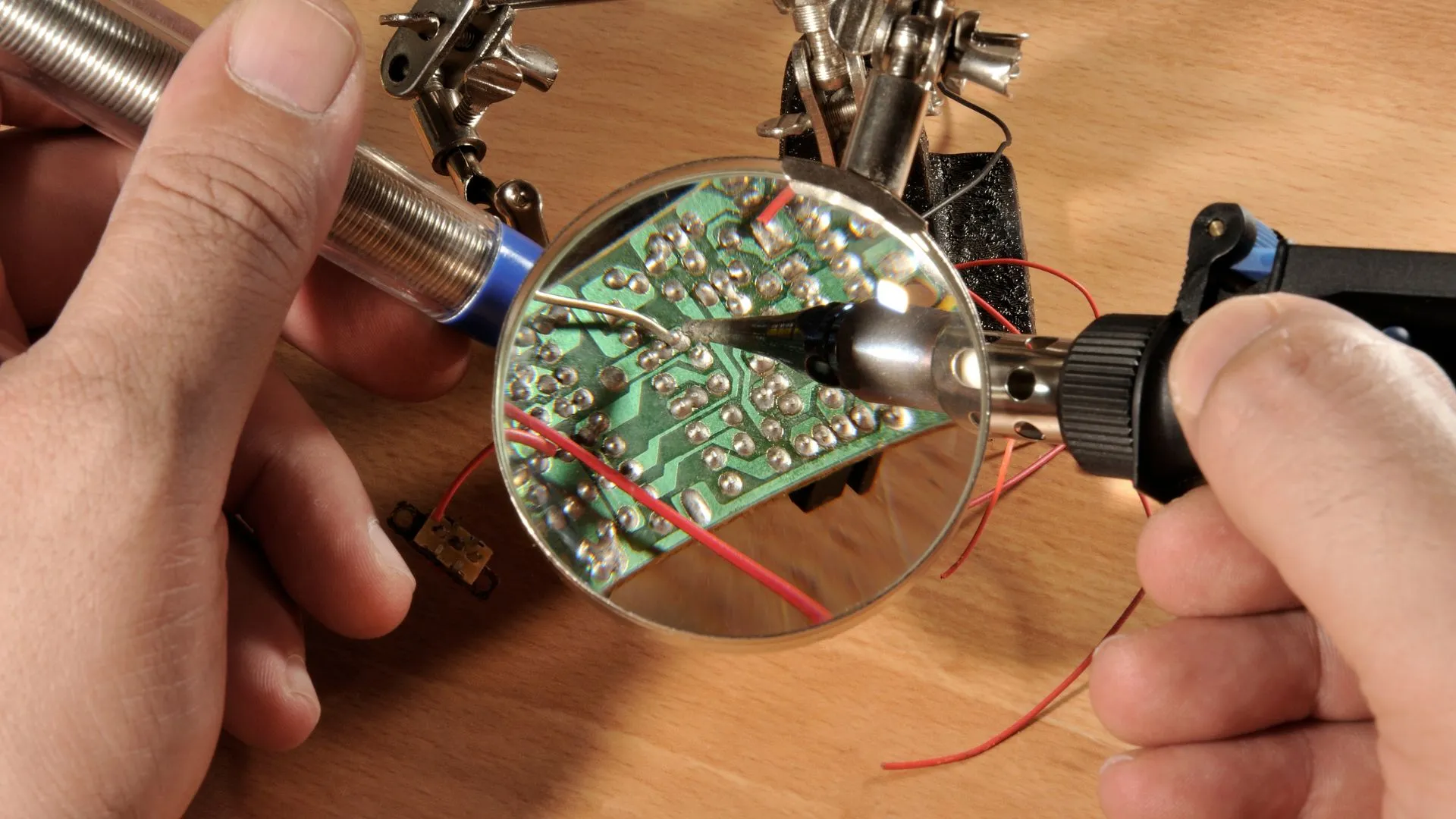
Solder Types Overview
- Lead-Free Solder:
- Complies with environmental standards like RoHS. Tin-silver-copper (Sn-Ag-Cu) alloys, e.g., SAC305, are common. Requires higher temperatures and has different mechanical properties than leaded solder.
- Leaded Solder:
- Contains tin and lead; formulations vary. Eutectic solder, e.g., Sn63Pb37, is used for precise temperatures. May offer lower melting points and better wetting.
- No-Clean Solder:
- Leaves minimal residue; no post-solder cleaning. Ideal for high-density PCBAs and sensitive components. Contains additives to reduce residue formation.
- Water-Soluble Solder:
- Removed with water-based solutions after soldering. Common in medical, automotive, and military electronics. Requires additional cleaning steps and careful drying to prevent corrosion.
- Rosin-Core Solder:
- Contains rosin flux core for oxide removal and wetting. Used in general-purpose soldering; available in lead-free and leaded. Common in hobbyist electronics, audio equipment.
- Activated Rosin Solder:
- Contains activators for enhanced flux activity. Ideal for difficult-to-solder surfaces with oxidation. May include halides, amines, or organic acids to boost effectiveness.
Our Soldering Solutions start with the use of high-quality solder alloys. We carefully select alloys that are compatible with a variety of components and assembly processes, ensuring reliable and durable solder joints.
Our experienced technicians employ precision soldering techniques to ensure accurate and controlled application. From hand soldering intricate components to using advanced reflow soldering methods, we tailor our approach to the specific requirements of your PCB design. In alignment with environmental standards, we offer lead-free soldering options. These alternatives maintain the integrity of solder joints while adhering to the latest industry regulations.
For large-scale production, we leverage automated soldering processes to ensure consistency and efficiency. Automated techniques, such as wave soldering and enhance throughput while maintaining the quality of solder joints.
.webp)
Indic Electronics boasts expertise in a wide range of soldering techniques. Whether your project requires hand soldering for precision or automated processes for efficiency, our team has the skills and experience to deliver.
We prioritize meticulous soldering practices to create connections that withstand the test of time and environmental conditions.
Our commitment to environmental responsibility is reflected in our lead-free soldering options. We ensure that our soldering solutions align with the latest industry standards and regulations. For projects with high production volumes, our automated soldering processes offer scalability without compromising on quality. These techniques maintain precision and consistency across large batches.
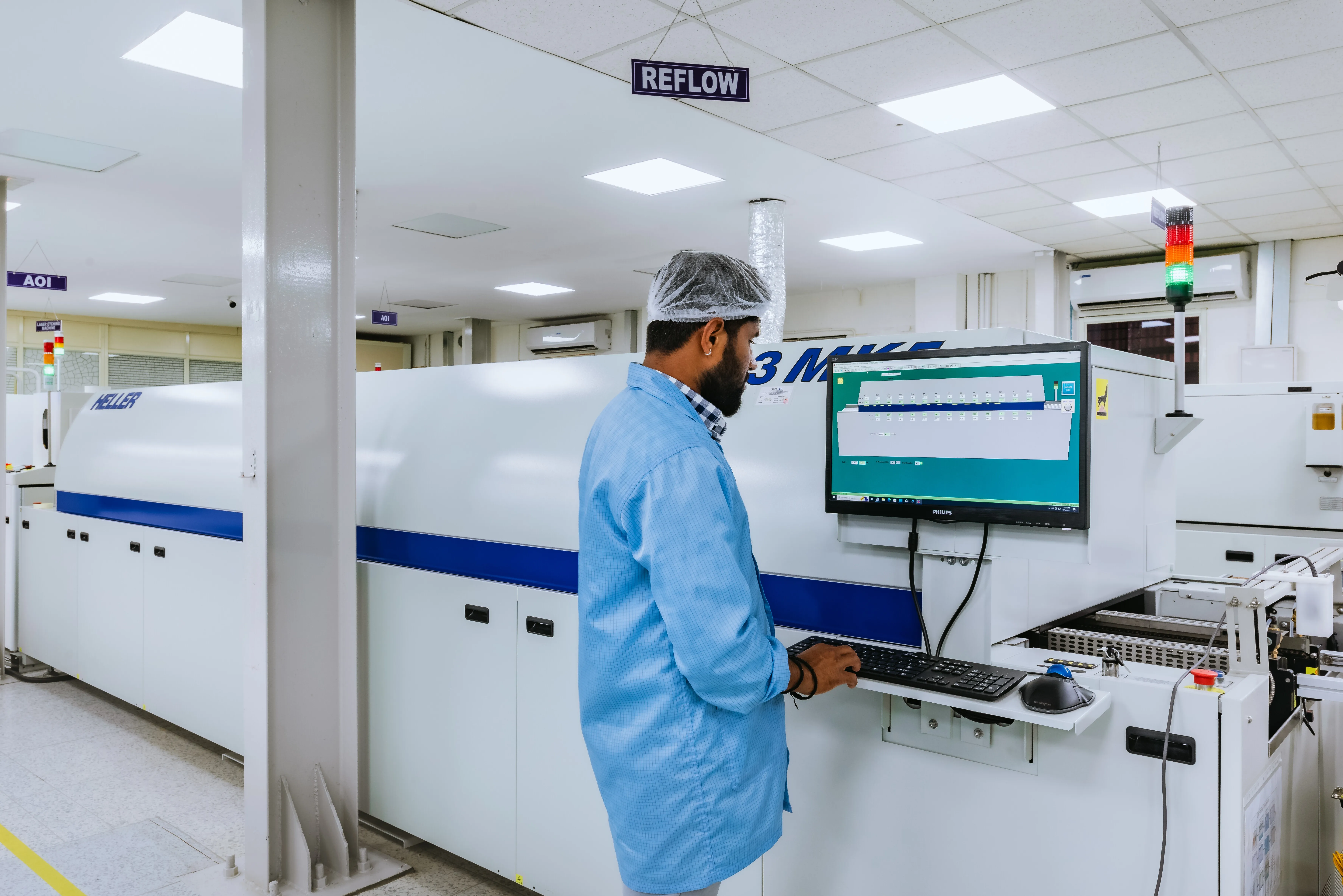
Solder flux is a chemical cleaning agent applied before soldering to remove oxides from metal surfaces, promoting better wetting and flow of the solder, and preventing re-oxidation during the soldering process.
Lead-Free Solder: Environmental friendly, commonly tin-copper or tin-silver-copper. Leaded Solder: Contains tin and lead, known for ease of use but less environmentally friendly. Silver Solder: Higher melting point, used for stronger joints.
Manual Soldering: For prototypes or repairs. Reflow Soldering: For surface-mount components. Wave Soldering: For through-hole and bulk components.
Clean the surfaces to be soldered. Apply flux to remove oxides and improve wetting. Heat the joint with a soldering iron. Apply solder directly to the joint, not the iron tip. Remove the iron and allow the joint to cool naturally.
Solder is typically made from a mixture of metals. Traditional solder contains lead (Pb) and tin (Sn), while lead-free solder, which is becoming standard, primarily consists of tin, with additives like copper, silver, and sometimes bismuth.
Solder creates a secure and conductive connection between electronic components and the PCB, ensuring the circuit functions as intended by facilitating electrical continuity.
Manual Soldering: Using a soldering iron for individual components. Reflow Soldering: Applying solder paste and heating the entire board to melt the paste, used for SMT components. Wave Soldering: Passing the PCB over a wave of molten solder, primarily for through-hole components.
The most commonly used solder in PCB assembly is a lead-free alloy, typically composed of tin (Sn), copper (Cu), and sometimes silver (Ag), in compliance with environmental regulations like RoHS.
PCB soldering is the process of joining electronic components to a printed circuit board (PCB) using solder, a fusible metal alloy, to establish a strong electrical connection between the component leads and the board's conductive pathways.