High Volume PCBA
High-volume Printed Circuit Board Assembly (PCBA) production involves efficiently manufacturing large quantities of PCBAs while maintaining high quality, reliability, and cost-effectiveness.
How does Indic do it?
Our cutting-edge manufacturing facility is equipped with advanced technology, enabling us to efficiently assemble high-quality, high-volume boards with quick turnaround times.
Design for Manufacturability (DFM)
Indic optimizes PCB designs for manufacturability, minimizing specialized components to reduce complexity and costs.
Automated Assembly
Indic uses automated equipment for high-throughput assembly, employing inspection systems like 3D AOI and SPI for defect detection.
Supply Chain Management
Indic builds strong supplier relationships, manages inventory efficiently, and minimizes lead times for a stable supply chain.
Lean Manufacturing
Indic applies lean principles, including JIT manufacturing and continuous improvement, to enhance efficiency and reduce waste.
Quality Control
Indic implements robust quality control processes, ensuring PCBAs meet high-quality standards through inspections and testing.
Process Optimization
Indic continuously monitors and optimizes manufacturing processes to improve efficiency, reduce costs, and enhance product quality.
Scalability and Flexibility
Indic designs adaptable production processes to handle demand fluctuations and changes in product requirements.
Worker Training
Indic invests in training for production personnel, empowering them to operate equipment effectively and contribute to process improvement.
From concept to completion, we offer end-to-end support for your high-volume PCB assembly needs. Our comprehensive services cover design optimization, prototyping, production, and rigorous quality control.
At Indic EMS Electronics, we believe in providing value for your investment. Our competitive pricing ensures that you receive high-quality, high-volume PCB assembly services without breaking the bank.
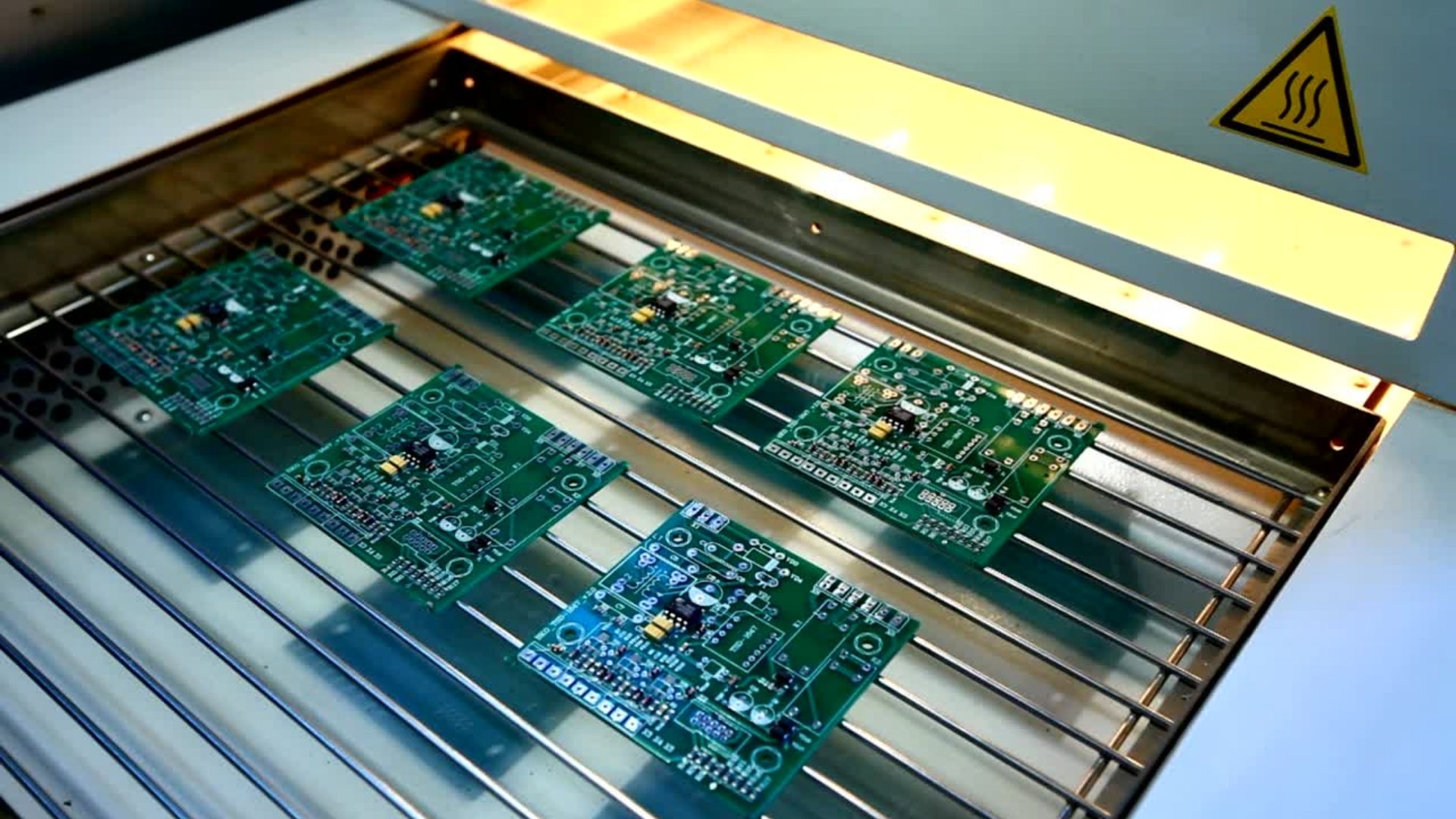
Our Capabilities
We offer high volume PCB assembly with surface mount technology as well as through hole selective soldering. In account of our use of jet solder paste printing, we offer quick turnaround time.
We are equipped with both hand soldering and machine soldering capabilities.
We fully analyze the BOM to ensure that all components are RoHS compliant for delivery.
Our robust testing includes the following methods based on requirements:
- 3D Automatic
- Optimal Inspection
-Solder Paste Inspection
- Functional Circuit testing
- X-Ray inspection
In addition, our strong design for testing protocol works well for high volume PCBs. The fact that we offer a sample for the quality of large batch turnkey orders.
Varies by manufacturer and application; standard sizes can go up to 18x24 inches, with most fitting within smaller dimensions for standard processes.
Single-sided Double-sided Multilayer Flexible Rigid Rigid-Flex
High frequency PCBs are designed to operate at frequencies typically above 1 GHz. They require specific materials and design considerations to minimize signal loss and maintain performance in applications like telecommunications and advanced computing.
Simplify design for manufacturability. Choose common, cost-effective components. Conduct extensive testing to reduce revisions.
High volume PCB assembly is crucial for meeting the demand of consumer electronics, reducing production costs, and achieving economies of scale. It enables widespread distribution of technology at lower prices.
High Volume: Ideal for mass-market products, offering cost benefits but requires significant design and testing investment. Low Volume: Suited for prototypes and small runs, providing flexibility and easy design adjustments at a higher cost per unit.