Functional Testing
A functional tester for Printed Circuit Board Assemblies (PCBAs) is a test system designed to verify the functionality and performance of electronic circuits after assembly. Functional testing is typically performed after soldering and assembly processes to ensure that the PCBAs meet the required specifications and perform as intended. Here's an overview of the components and functionality of a functional tester for PCBA:
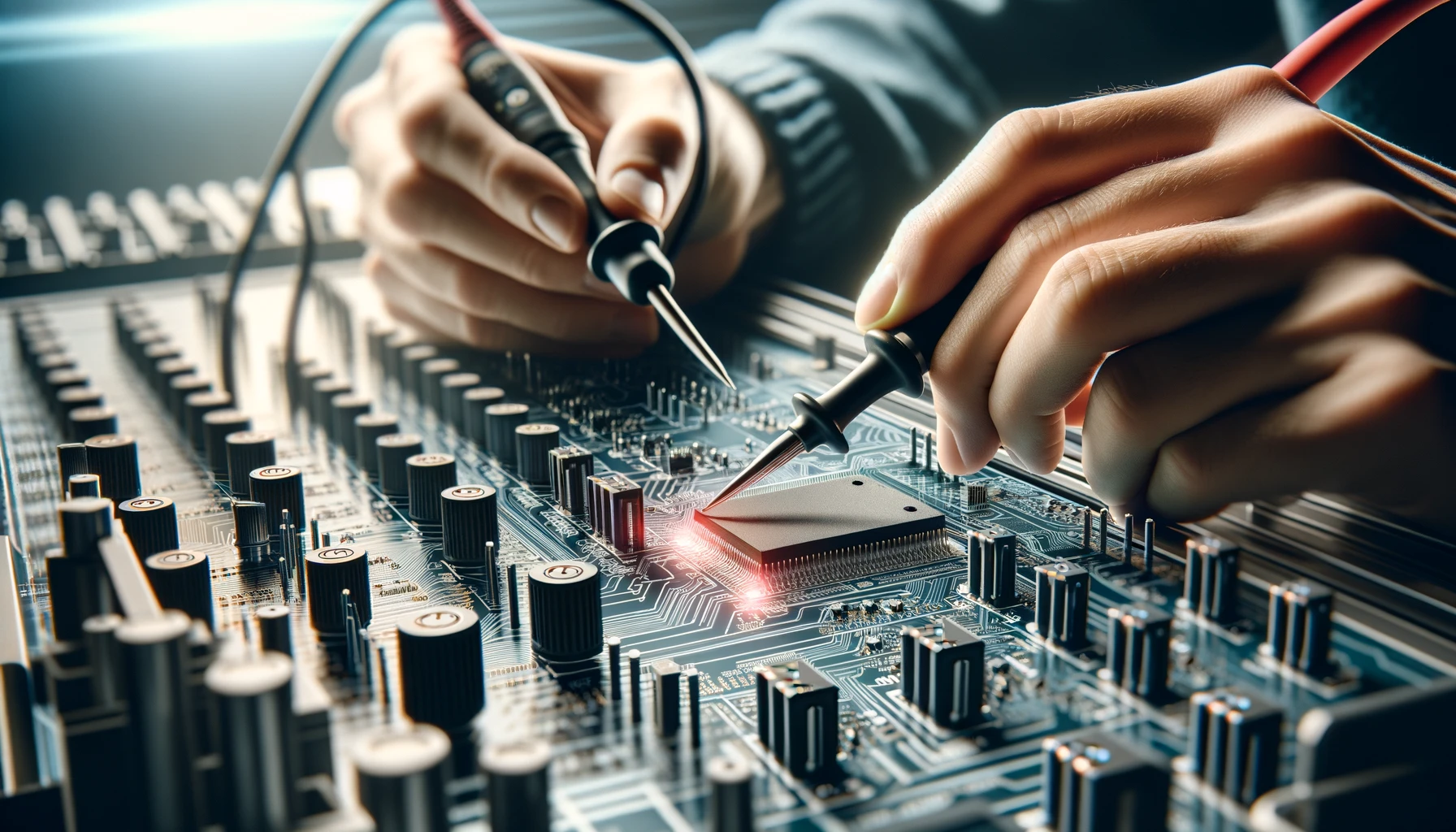
Testing Setup Overview
- Test Fixtures:
- Custom-designed fixtures for secure PCB placement during testing.
- Ensures accuracy and repeatability in line with PCB form factor and layout.
- Test Software:
- Controls functional tester operation and executes tailored test routines.
- Includes predefined sequences, algorithms, and scripts for specific PCBA requirements.
- Provides data logging, result analysis, and reporting features.
- Instrumentation:
- Functional testers equipped with diverse instruments like DMMs, oscilloscopes, power supplies.
- Measures voltages, currents, waveforms, and frequencies to validate PCBA functionality.
- Interface Hardware:
- Provides electrical connections between test fixtures, instruments, and the PCBA.
- Includes connectors, cables, relays, switches, and signal conditioning circuits.
- User Interface:
- Graphical or text-based interface for configuring tests, monitoring progress, and viewing results.
- Features test selection menus, parameter settings, status indicators, and result displays.
- Functional Test Coverage:
- Performs varied functional tests, including POST, signal processing, communication interfaces, sensor calibration, and more.
- Scalability and Flexibility:
- Adaptable to changes in PCB designs, test needs, and production volumes.
- Modular architectures and configurable setups support evolving testing requirements and multiple product variants on one platform.
Our approach to functional testing is rooted in precision and efficiency. We employ a combination of automated and manual testing methods to meticulously evaluate every aspect of your electronic devices. Our team of experienced technicians utilizes advanced testing equipment and follows industry best practices to simulate real-world scenarios and identify potential issues.
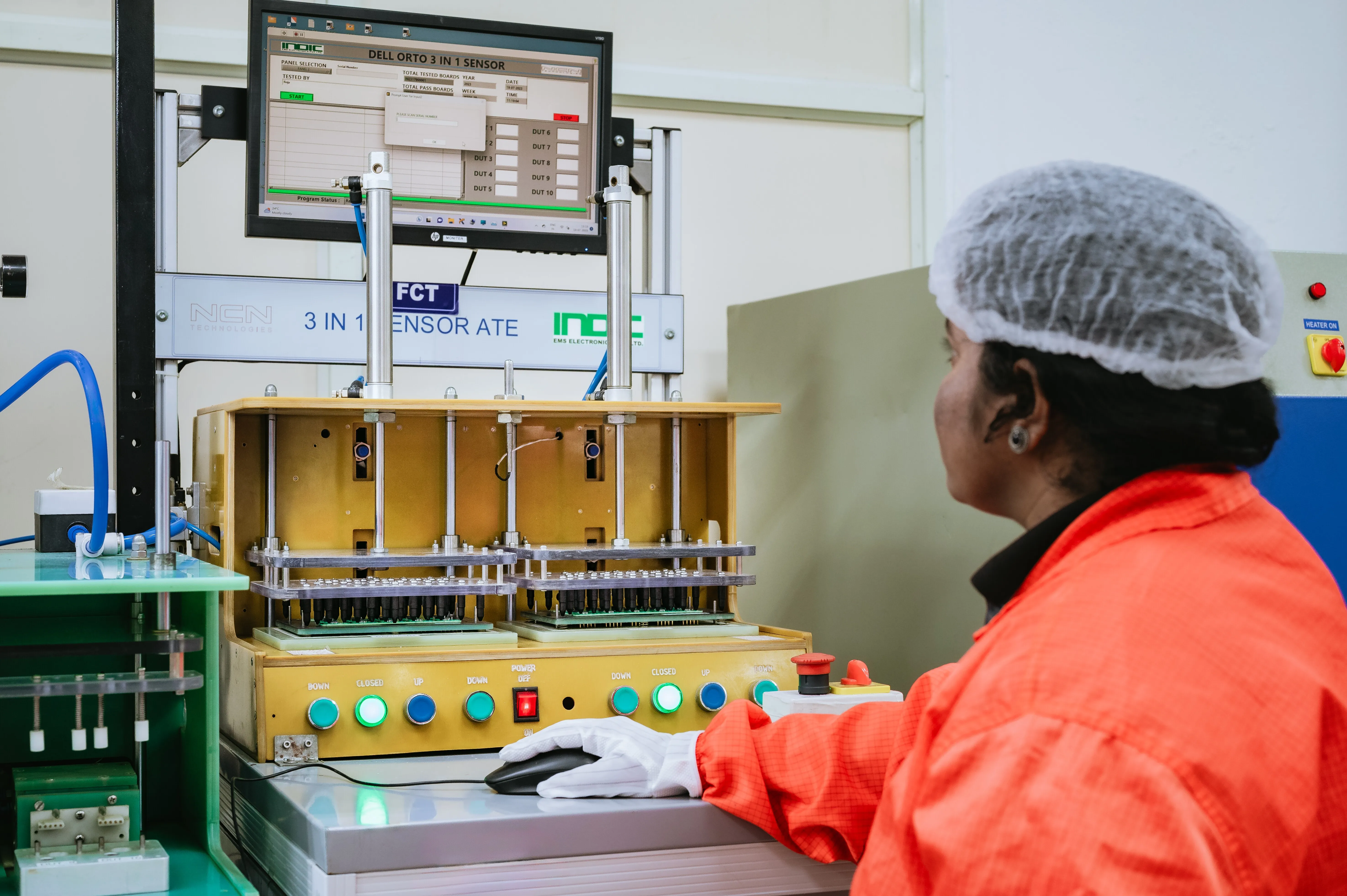
We leave no stone unturned. Our testing procedures are exhaustive, covering a wide range of functionalities to ensure that your electronic devices meet the highest standards of quality and reliability. Indic Electronics is equipped with cutting-edge testing facilities and advanced tools. Our commitment to staying abreast of technological advancements ensures that we provide testing services that align with the latest industry standards.
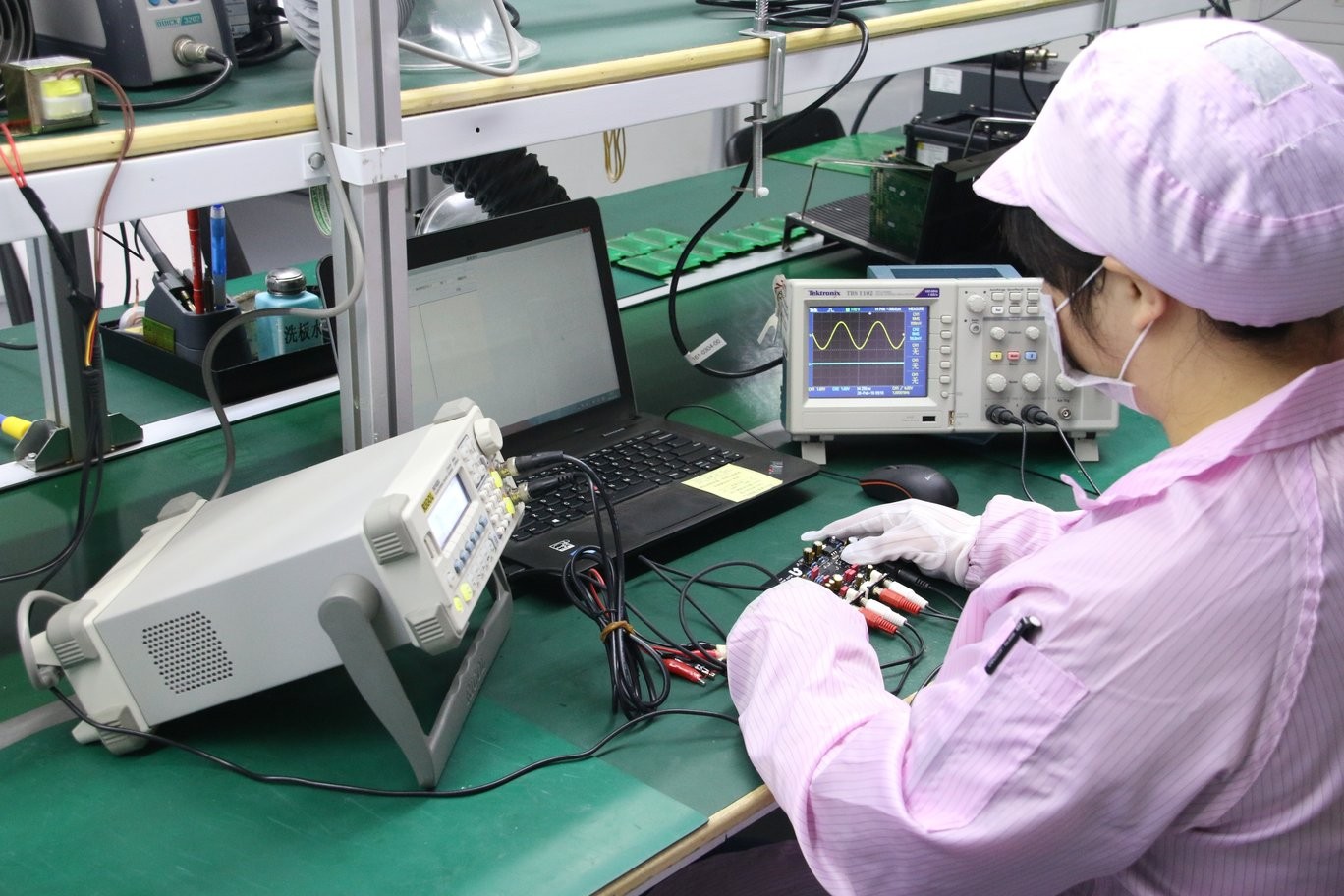
- Our team of qualified test engineers continually evaluate & develop test printed circuit boards and assemblies.
- Functional testing requires instruments such as I/O PCBs, communication ports, digital multimeters and more.
- Normally, the testing is done according to test procedures and specifications mentioned by test engineer.
- With the tester connected to the PCB through a probe point, it stimulates the electrical environment of the PCB.
- It therefore ensures that the testing is full proof and any flaws in either design or functionality is brought to light, thereby ensuring there are no costly mistakes at a later date.
If a PCB fails functional testing: The failure is analyzed to determine the cause (component, assembly process, design issue). The PCB may undergo rework or repair to correct the identified issue. After repairs, the PCB is retested to ensure it now passes functional testing, verifying its readiness for final assembly.
Functional testing can identify a wide range of defects, including: Incorrect component installation (wrong orientation or placement). Faulty components (damaged or non-operational parts). Soldering issues (cold joints, solder bridges). Missing components or incorrect component values. Short circuits or open circuits within the PCB.
Functional testing is conducted by applying specific inputs to the PCB and measuring the outputs to compare against expected results. Test equipment may include signal generators, power supplies, and measurement devices, configured according to the PCB's operational specifications.
Functional testing is crucial in PCB assembly because it: Ensures the assembled PCB meets the design requirements. Identifies manufacturing defects or component failures. Guarantees product reliability and quality before market release.
PCB functional testing services are offered by EMS providers to test assembled PCBs for proper functionality. These services use specialized equipment and test setups to simulate operational conditions and verify product performance against specified criteria.
PCB functional testing is a process where a printed circuit board (PCB) assembly is tested for its intended operation. It ensures that all components and circuits on the PCB work correctly together as designed.
Functional testing in the Electronics Manufacturing Services (EMS) industry involves verifying that a completed electronic assembly, such as a PCB, operates according to its design specifications. This test checks the functionality of the device under test (DUT) by simulating its operational environment.