BGA
A Ball Grid Array (BGA) is a type of surface-mount packaging used for integrated circuits (ICs) and other semiconductor devices. In a BGA package, the connections between the integrated circuit and the printed circuit board (PCB) are made through an array of solder balls located on the underside of the package. These solder balls serve as the connection points and are arranged in a grid pattern, hence the name "Ball Grid Array."
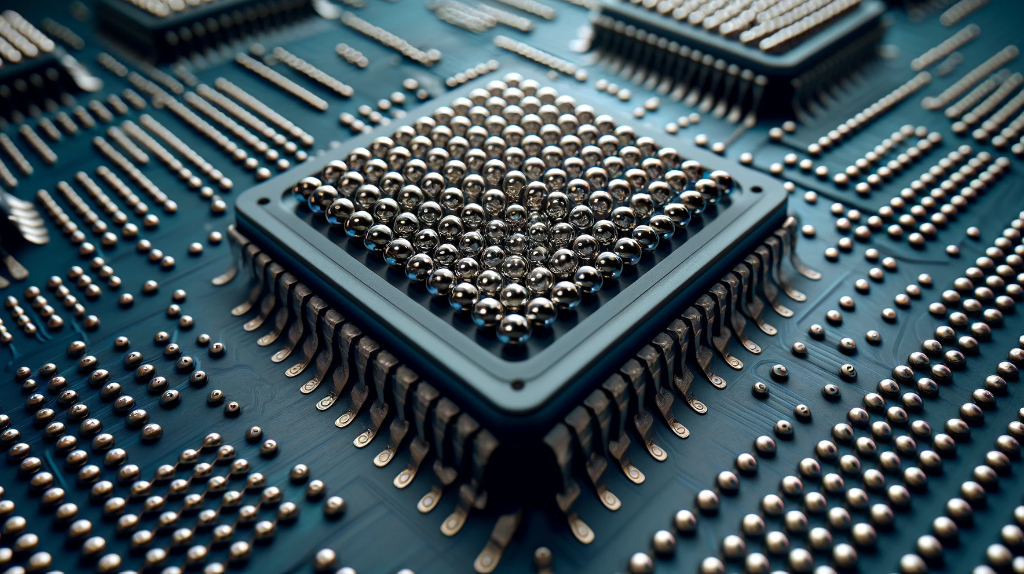
Types of BGA
- Ceramic BGA (CBGA):
- Uses a ceramic substrate for excellent thermal and mechanical properties.
- Ideal for high-performance applications in aerospace, military, and telecommunications systems.
- Plastic BGA (PBGA):
- Utilizes a plastic substrate, offering cost-effectiveness.
- Suitable for consumer electronics with various sizes and configurations.
- Flip-Chip BGA (FCBGA):
- Employs a flip-chip bonding technique for improved electrical performance.
- Commonly used in high-speed applications like microprocessors and graphics processors.
- Tape Ball Grid Array (TBGA):
- Uses adhesive tape for temporary solder ball placement during assembly.
- Enhances handling and placement efficiency, reducing the risk of solder ball damage.
- Stud BGA (SBGA):
- Features metal studs or posts for electrical connections.
- Provides enhanced mechanical stability, ideal for automotive electronics and ruggedized devices.
-
- Micro BGA (µBGA):
- Has smaller ball pitches for higher I/O density and device miniaturization.
- Commonly used in mobile devices and portable electronics where space is limited.
BGA components require a specialized soldering process, and our reflow soldering techniques are tailored to meet the unique challenges of BGA assembly. This method ensures reliable solder joints for enhanced durability and performance.
X-ray Inspection for BGA Quality: To ensure the integrity of BGA assemblies, we employ X-ray inspection technology. This allows for non-destructive testing of the solder joints beneath the BGA components, any potential defects or discrepancies.
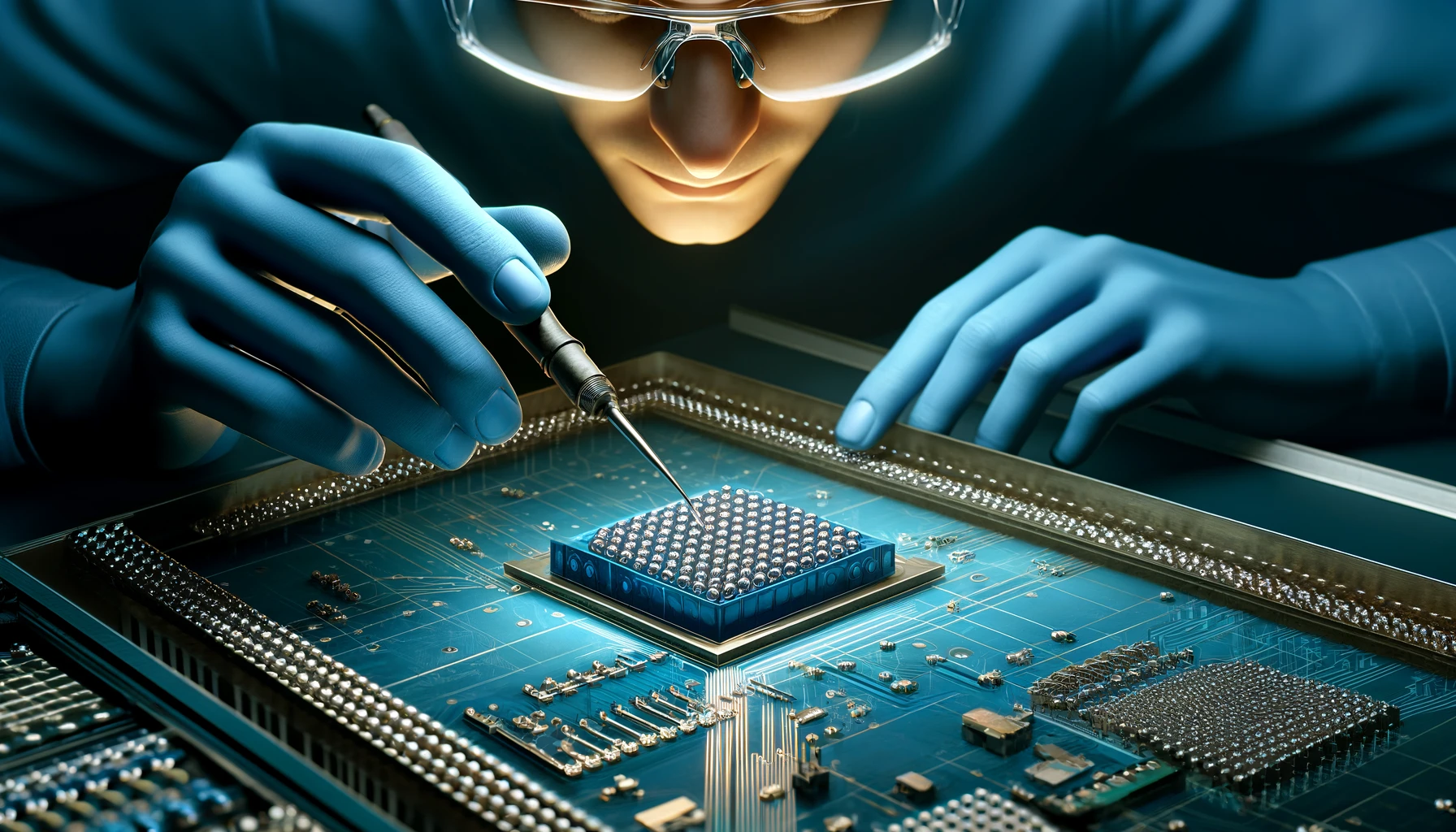
Our BGA assembly services are versatile and flexible, accommodating various BGA component types and sizes.
The combination of rigorous quality control measures, X-ray inspection, and adherence to industry standards guarantees the reliability and performance of the final assembled products.
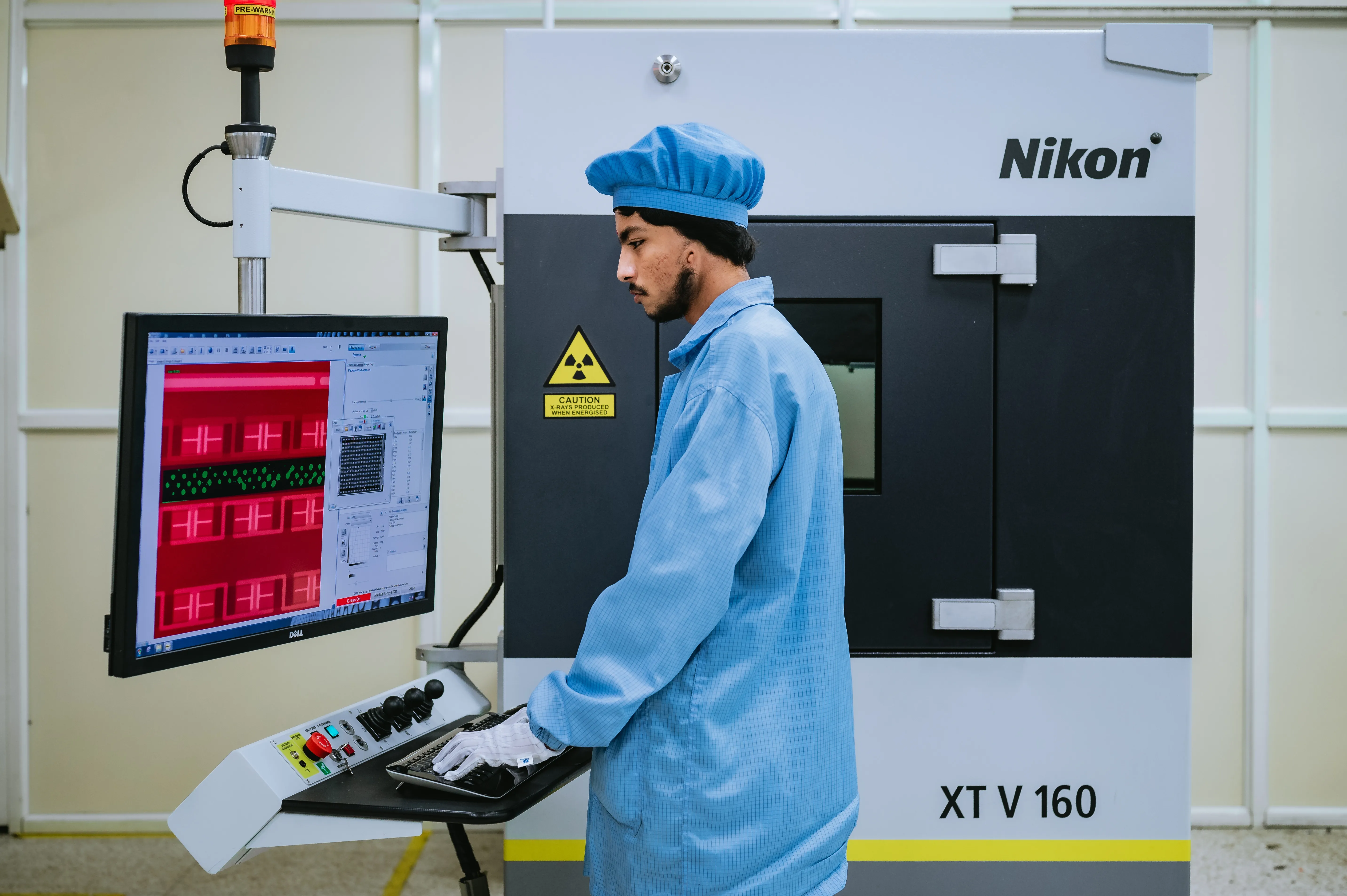
A BGA package is a type of surface mount packaging for integrated circuits that uses a grid of solder balls as its connectors. These solder balls provide the electrical connections to the PCB, enabling a compact and high-density connection layout.
BGA stands for Ball Grid Array, a type of surface mount packaging used for integrated circuits. BGA packages use solder balls arranged in a grid on the bottom of the package for electrical and mechanical connection to the PCB.
BGA reballing is the process of removing old solder balls from a BGA component and replacing them with new ones. This repair technique is used to fix defective BGA solder joints or to reattach a BGA component to a PCB.
In SMT (Surface Mount Technology), BGA refers to a type of packaging used for surface-mounted devices where solder balls on the underside of the package provide the electrical connections to the PCB, allowing for high-density connections.
BGA is important in PCB assembly for enabling high-density connections, reducing PCB size, and enhancing electrical performance. Its solder ball array allows for efficient manufacturing and reliable electrical connections, critical for modern, high-performance electronics.
There are several types of BGA, including PBGA (Plastic Ball Grid Array), CBGA (Ceramic Ball Grid Array), TBGA (Tape Ball Grid Array), and MBGA (Micro Ball Grid Array), each differing in materials and specific applications.
BGA is used in PCBs to achieve higher density connections, allowing more pins in less space compared to traditional packaging. This is crucial for modern electronic devices that require compact size with high functionality.
BGA is used for its ability to provide a large number of interconnections in a small space, improving performance and reducing size. The solder balls offer better joint reliability and heat conduction, suitable for high-performance and compact electronic devices.
The process of BGA production includes creating the BGA package with solder balls arranged in a grid pattern, placing the BGA on the PCB with precise alignment, and then soldering it using reflow soldering technique to create a solid mechanical and electrical bond.
A BGA chipset refers to a chipset packaged in a Ball Grid Array format. It is used in various electronic devices, such as computers and smartphones, for its efficient space utilization and reliable connections.
BGA assembly is the process of attaching Ball Grid Array (BGA) components to a printed circuit board (PCB) using surface mount technology (SMT) techniques. It involves applying solder paste, placing BGA components, and using reflow soldering to establish the connections.