Design for Product Packing
Design for Product Packaging (DfPP) refers to the practice of integrating considerations of packaging requirements and constraints into the overall product design process. It involves designing products with packaging in mind from the outset to ensure that the packaging effectively protects, transports, and presents the product while also aligning with branding and sustainability goals as per ISTA standards.
At Indic, we believe in proactive and integrated DfPP:
Early Collaboration: We collaborate with you from the initial design stages, considering packaging needs and constraints alongside product functionality.
DFPP Expertise: Our team leverages extensive DfPP knowledge to suggest design modifications that optimize packaging efficiency and minimize materials.
Software and Simulation: We utilize advanced software and simulation tools to test and validate packaging designs virtually, ensuring optimal protection and minimizing physical prototyping needs.
Sustainability Focus: We prioritize eco-friendly packaging solutions whenever possible, recommending recycled materials and minimizing waste, while still adhering to ISTA standards for safe transportation.
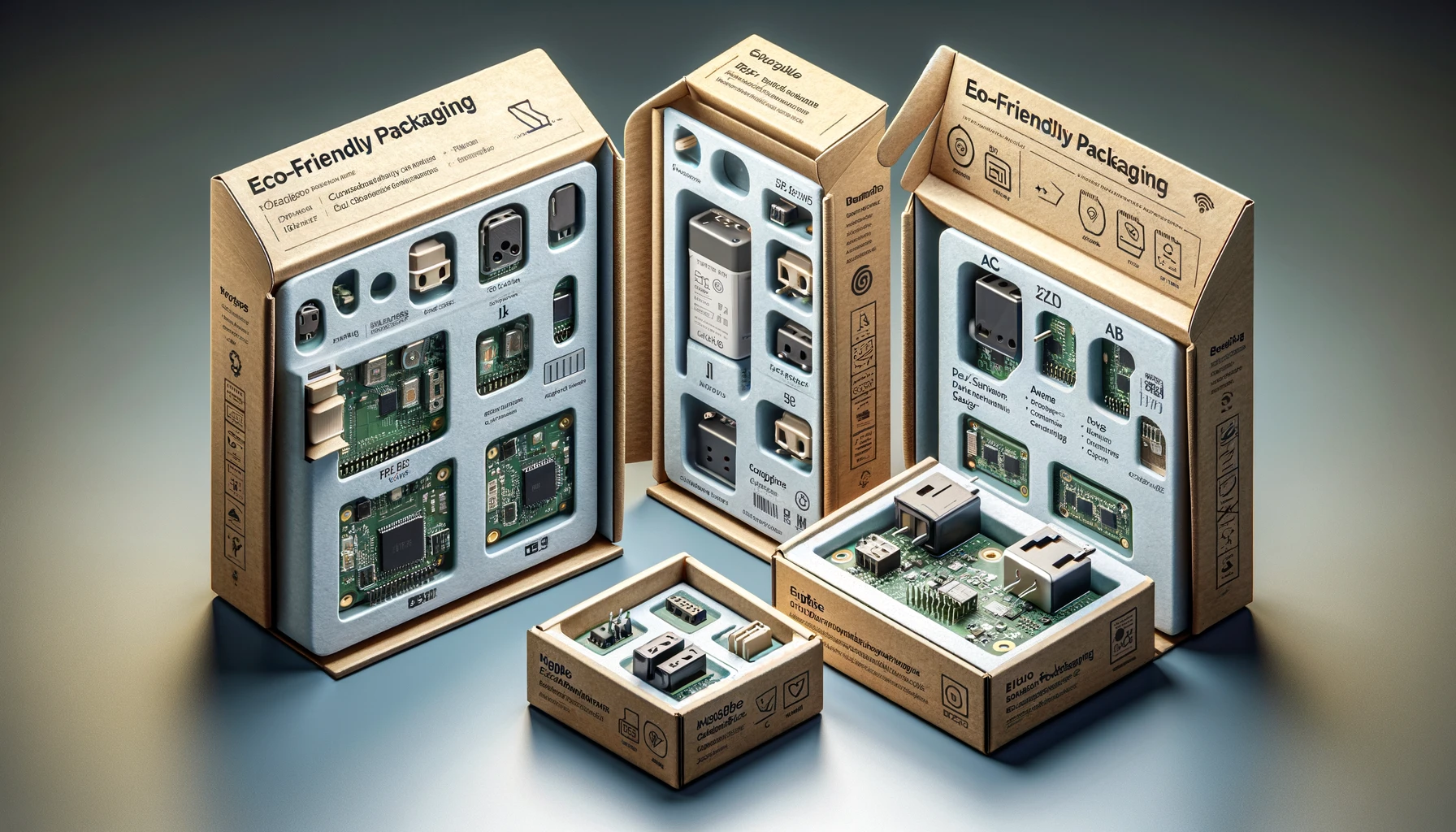
Our DfPP expertise ensures your product arrives safe and undamaged, minimizing potential returns and costs. We help you optimize packaging size and material usage, leading to cost savings and a smaller environmental footprint.
Well-designed packaging enhances the unboxing experience for your customers, fostering brand loyalty.
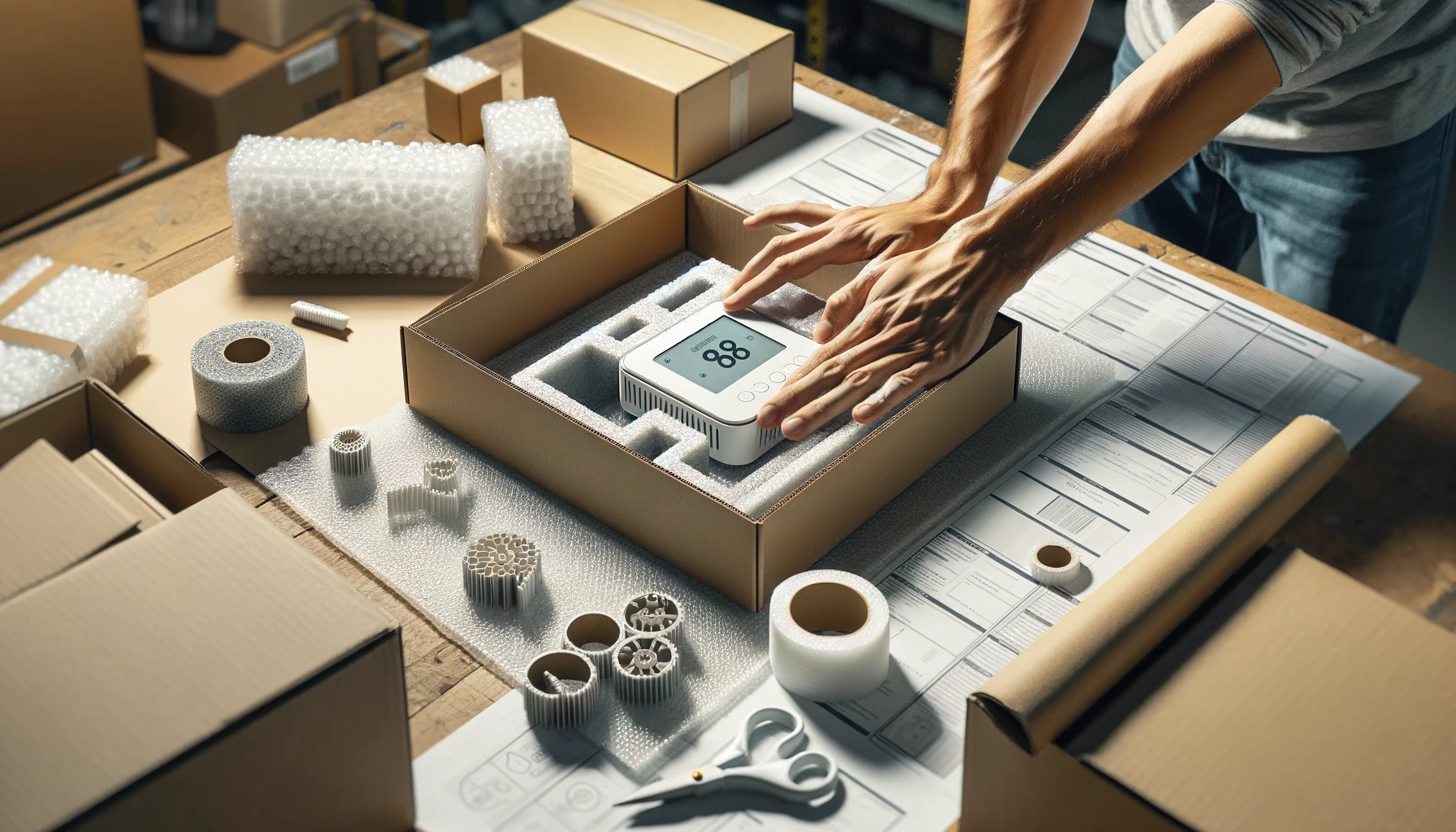
Our Capabilities
- Product Protection
- Functional Design
- Brand Identity
- Sustainability
- Regulatory Compliance
- Innovative Materials and Technologies
To package a PCB, first clean and inspect it, then place it in an anti-static bag. Wrap it with bubble wrap or foam for shock absorption, and secure it in a sturdy box with cushioning materials. Finally, seal the box and label it with handling instructions and ESD warnings.
PCB packaging is vital for protecting the board from physical damage, electrostatic discharge (ESD), and environmental factors like moisture. It also ensures compliance with shipping regulations and reflects the brand's quality commitment.
Desiccants in PCB packaging absorb moisture, preventing condensation and corrosion on the PCB during shipping and storage, thus preserving its functionality and longevity
Typical PCB packaging materials include anti-static bags to prevent ESD damage, bubble wrap or foam for cushioning, corrugated cardboard boxes for external protection, desiccants to absorb moisture, and sealing tape and labels.