pFMEA
Process Failure Mode and Effects Analysis (PFMEA) is a structured method used to identify and prioritize potential failure modes in a manufacturing or assembly process, evaluate their potential effects, and develop mitigation strategies to prevent or minimize their impact.
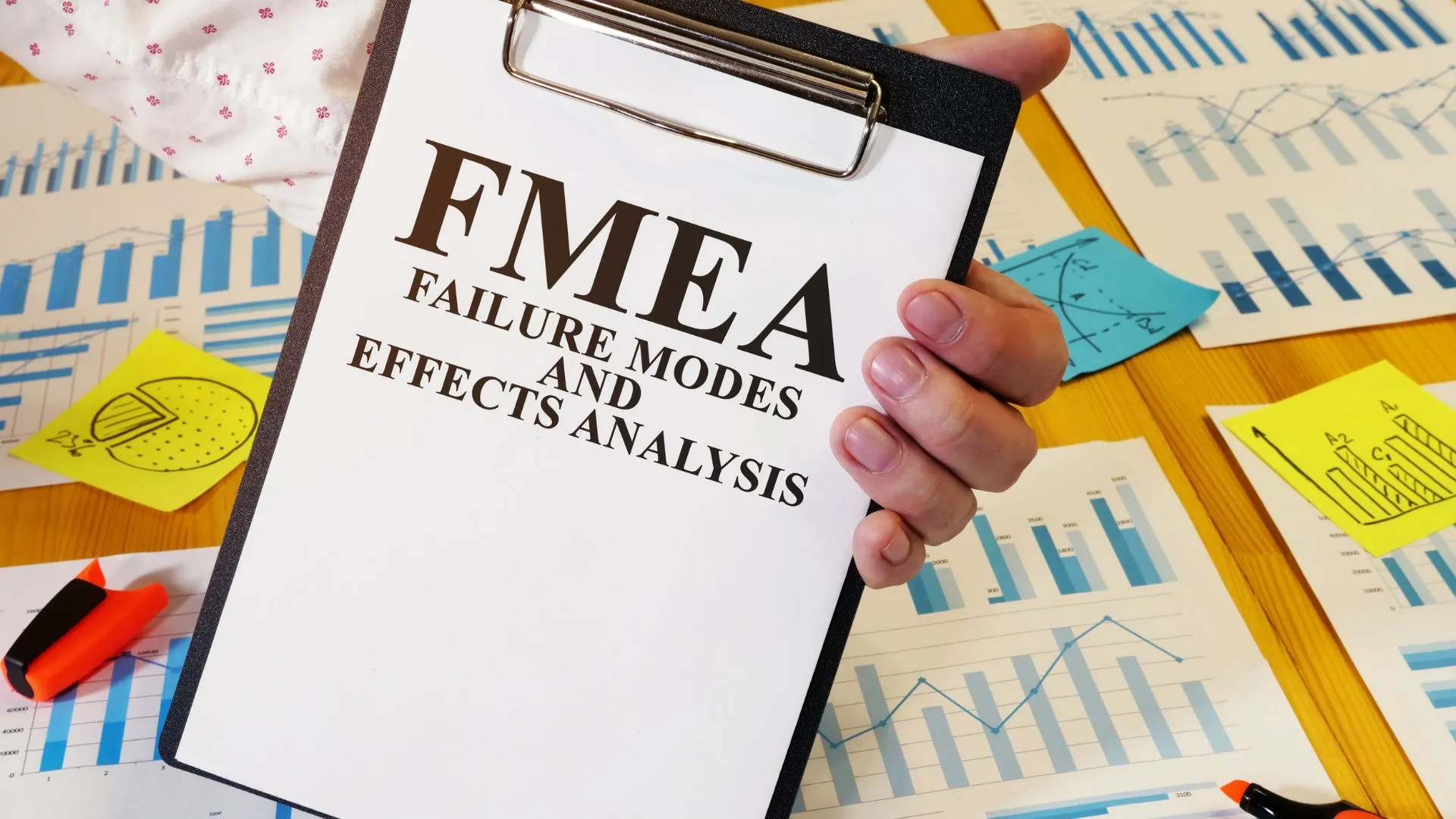
Here's how Indic actively conducts PFMEA:
Indic actively conducts PFMEA by first pinpointing specific manufacturing or assembly processes such as PCB assembly, injection molding, machining, or welding. A cross-functional team is then assembled, comprising process experts and representatives from quality assurance, engineering, production, and relevant departments. Each process is meticulously broken down into individual steps to ensure a comprehensive analysis of potential failure modes. Through active brainstorming sessions, Indic explores various failure modes considering factors like equipment malfunction, operator error, material defects, and environmental conditions.
Indic evaluates the effects of each failure mode on product quality, safety, reliability, cost, and customer satisfaction, assigning severity ratings on a numerical scale accordingly. Root cause analysis techniques such as the 5 Whys or fishbone diagrams are employed to determine the underlying causes of failure modes.
Assessing the likelihood of each failure mode occurring and being detected is a proactive step for Indic, drawing on historical data, experience, and expert judgment. The Risk Priority Number (RPN) is then calculated for each failure mode, guiding the prioritization of mitigation efforts. Indic prioritizes high-risk failure modes for corrective and preventive actions, which may involve process adjustments, equipment upgrades, or training initiatives.
Continuous monitoring and review of implemented strategies ensure their ongoing effectiveness. The PFMEA is dynamically updated to reflect changes in process, technology, or customer requirements. Indic's proactive approach to PFMEA underscores its commitment to quality, safety, and continuous improvement in manufacturing processes.
In our commitment to delivering high-quality electronic products, we integrate pFMEA into our manufacturing processes as a proactive measure. Our approach involves a collaborative effort among cross-functional teams, including engineers, quality assurance specialists, and production experts.
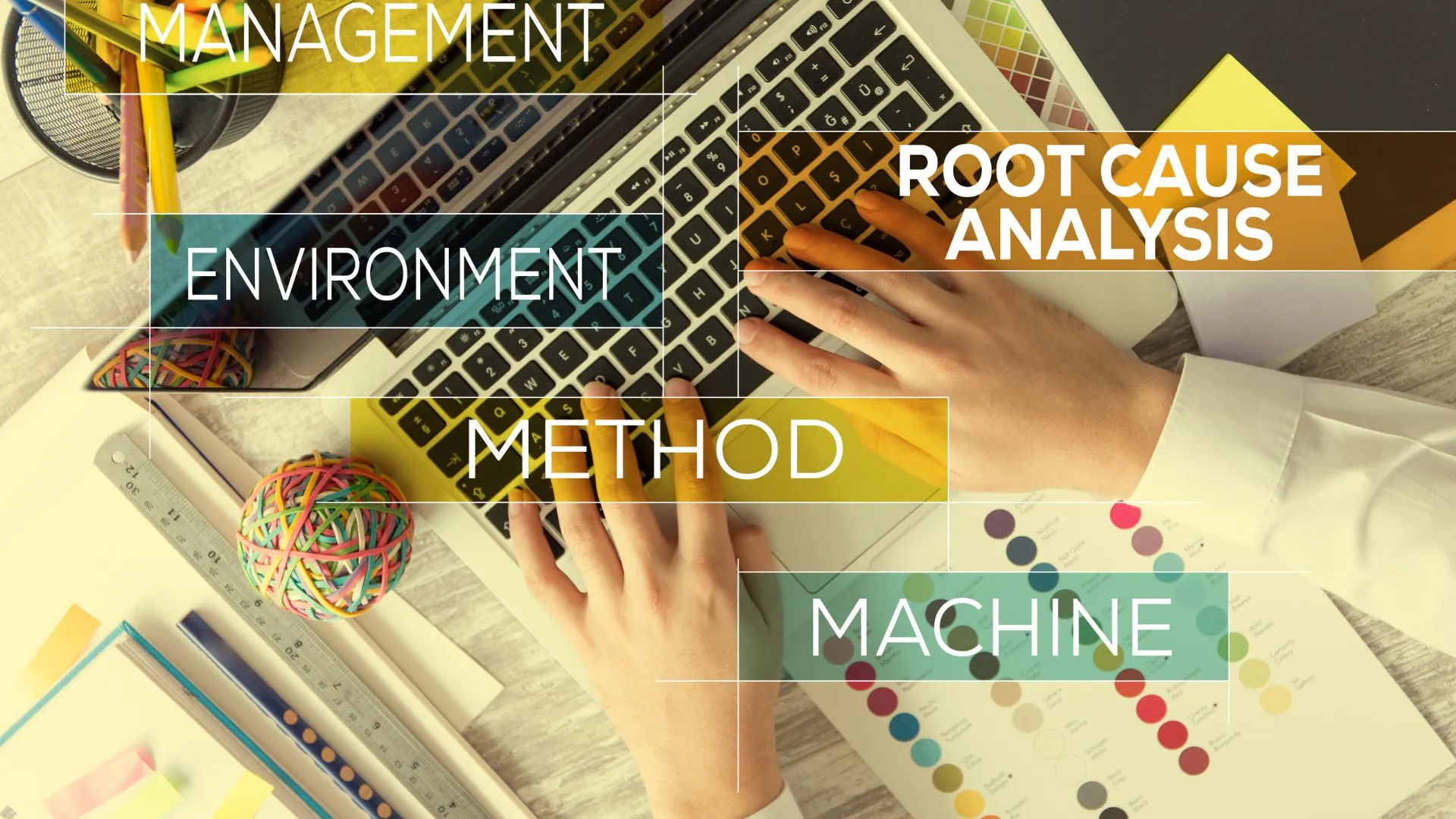
Our Capabilities
- Risk Assessment
- Critical Thinking
- Process Understanding
- Cross-Functional Collaboration
- Data Analysis
- Risk Prioritization
- Root Cause Analysis
- Mitigation Planning
- Implementation and Monitoring
- Documentation and Reporting
- Regulatory Compliance
- Continuous Improvement
Yes, PFMEA (Process Failure Mode and Effects Analysis) is a proactive quality tool used in the manufacturing industry to identify and mitigate potential failures in a process before they occur, enhancing product quality and reliability.
PFMEA, or Process Failure Mode and Effects Analysis, is a structured approach to identify, prioritize, and mitigate risks in a manufacturing process, aiming to improve quality and reliability by preventing process-related failures.
The three types of FMEA are Design FMEA (DFMEA), which focuses on potential failures in product design; Process FMEA (PFMEA), which identifies potential failures in manufacturing processes; and System FMEA (SFMEA), which analyzes failures at the system or subsystem level.
An early PFMEA is important because it allows for the identification and mitigation of potential process failures before they become costly or dangerous, leading to a more efficient, reliable, and safe manufacturing process.
Using a PFMEA involves mapping out each step of the manufacturing process, identifying potential failure modes, assessing their impact and likelihood, prioritizing them based on risk, and implementing control measures to mitigate or eliminate these risks.
PFMEA (Process FMEA) focuses specifically on identifying and reducing risks in manufacturing processes, while FMEA is a broader term that can refer to Design FMEA (DFMEA), Process FMEA (PFMEA), or System FMEA (SFMEA), each targeting different aspects of product and process reliability.
PFMEA (Process Failure Mode and Effects Analysis) is a systematic analytical tool used to identify and address potential failures in a manufacturing or assembly process. It's used by creating a step-by-step analysis for each process component, identifying potential failure modes, assessing their impact, and implementing mitigation strategies.
Design FMEA (DFMEA) focuses on potential design-related failures and their effects on product performance, while Process FMEA (PFMEA) targets potential failures in the manufacturing process and their impact on product quality.
The main types of FMEAs are Design FMEA (DFMEA), Process FMEA (PFMEA), and System FMEA (SFMEA), each analyzing risks at different stages of product development and manufacturing to enhance reliability and safety.
An example of PFMEA in manufacturing could involve the assembly line for electronic devices, where PFMEA helps identify potential issues like incorrect component placement or soldering defects, allowing for preventive measures to be implemented.