Solderability Issues
Identify and eliminate susceptible areas where there will be insufficient solder, solder splashes, solder shorts or non robust solder joints for SMT and PTH process
Indic proactively combats solderability issues in SMT and PTH processes. Our DFM review identifies potential problems early. This includes analyzing factors like pad size and shape, component placement, and thermal profiles. We use high-quality materials, advanced equipment, and rigorous inspection throughout the process. By continuously improving, we minimize defects, enhance product quality, and ensure production efficiency. Choose Indic for reliable soldering solutions and peace of mind.
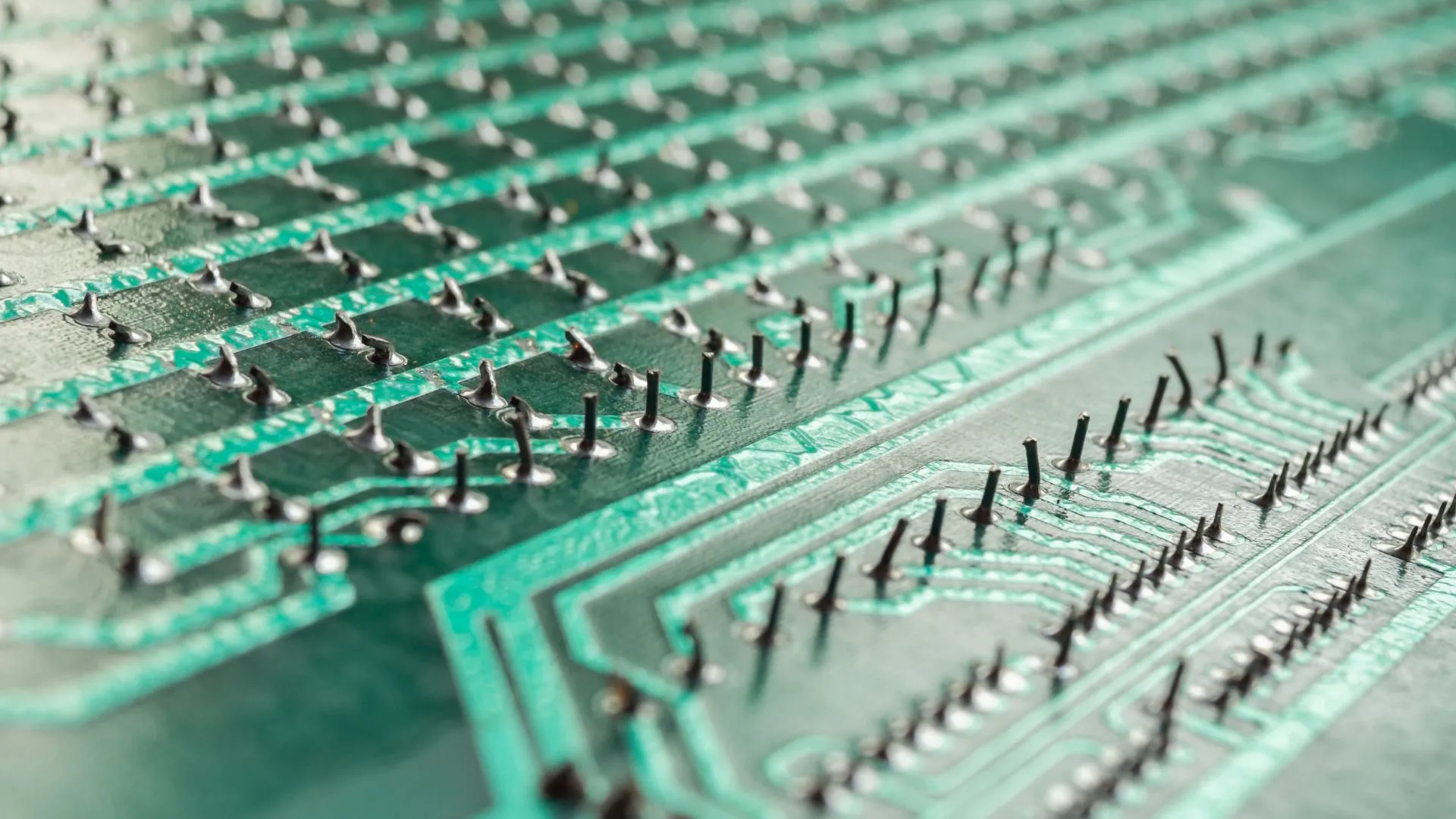
At Indic, we excel in identifying and eliminating potential solderability issues in Surface Mount Technology (SMT) and Plated Through-Hole (PTH) processes. Our proactive approach begins with a thorough Design for Manufacturability (DFM) review, where we analyze factors such as pad size and shape, component placement, and thermal profiles to mitigate any foreseeable problems early on. We prioritize quality at every step, utilizing high-quality materials, state-of-the-art equipment, and stringent inspection processes throughout the soldering process. With our continuous improvement efforts, we minimize defects, enhance product quality, and ensure production efficiency, giving you peace of mind.
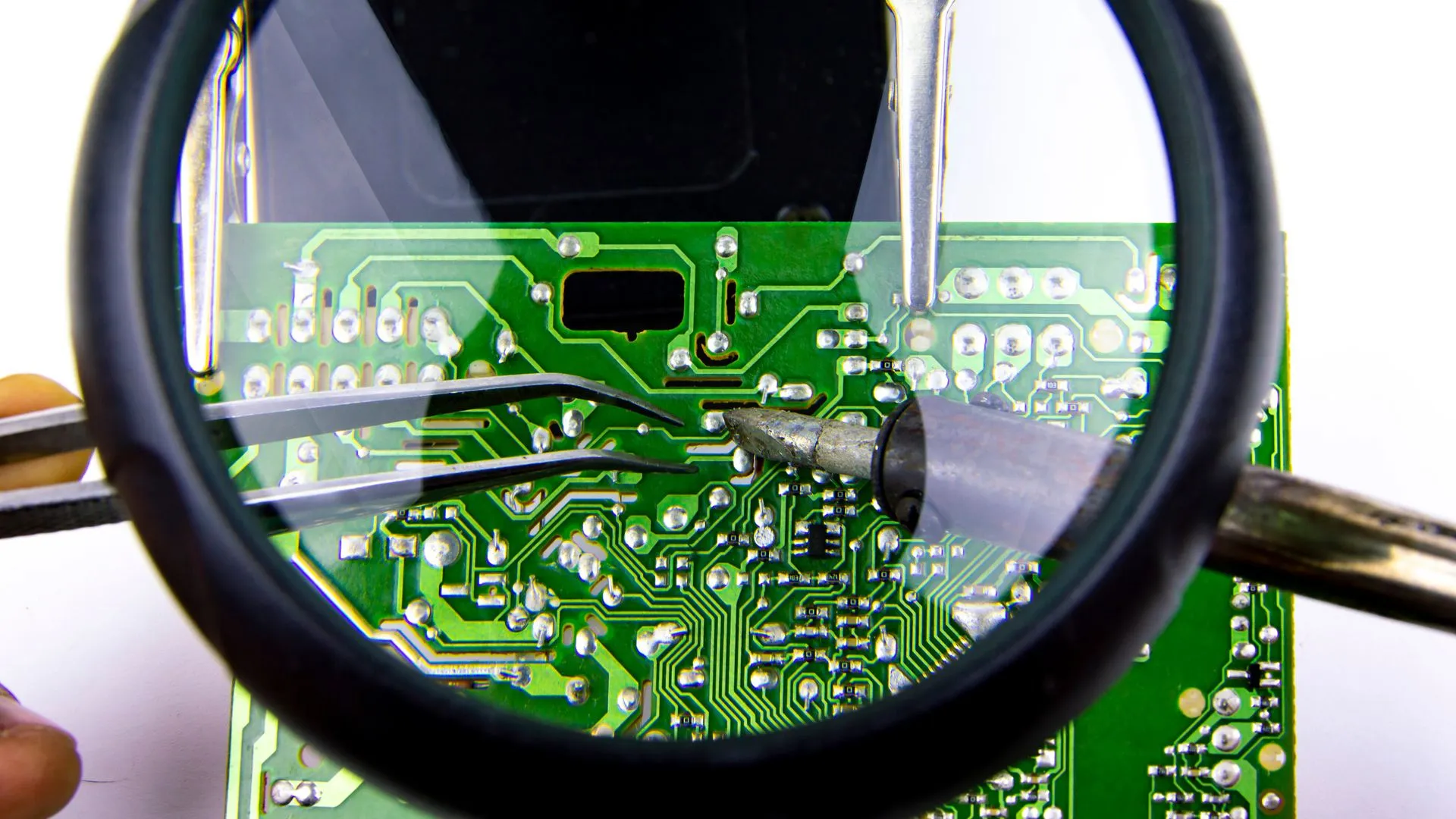
- SMT Soldering
- Wave soldering
- Auto soldering
- Selective soldering
- Manual soldering
- X-Ray Inspection
- 100X Scope Inspection to defect validation