Process Development
Process development for Printed Circuit Board Assemblies (PCBAs) involves establishing the manufacturing processes and procedures necessary to efficiently and reliably produce high-quality PCBAs. This process is critical for ensuring consistency, repeatability, and quality in PCB assembly.
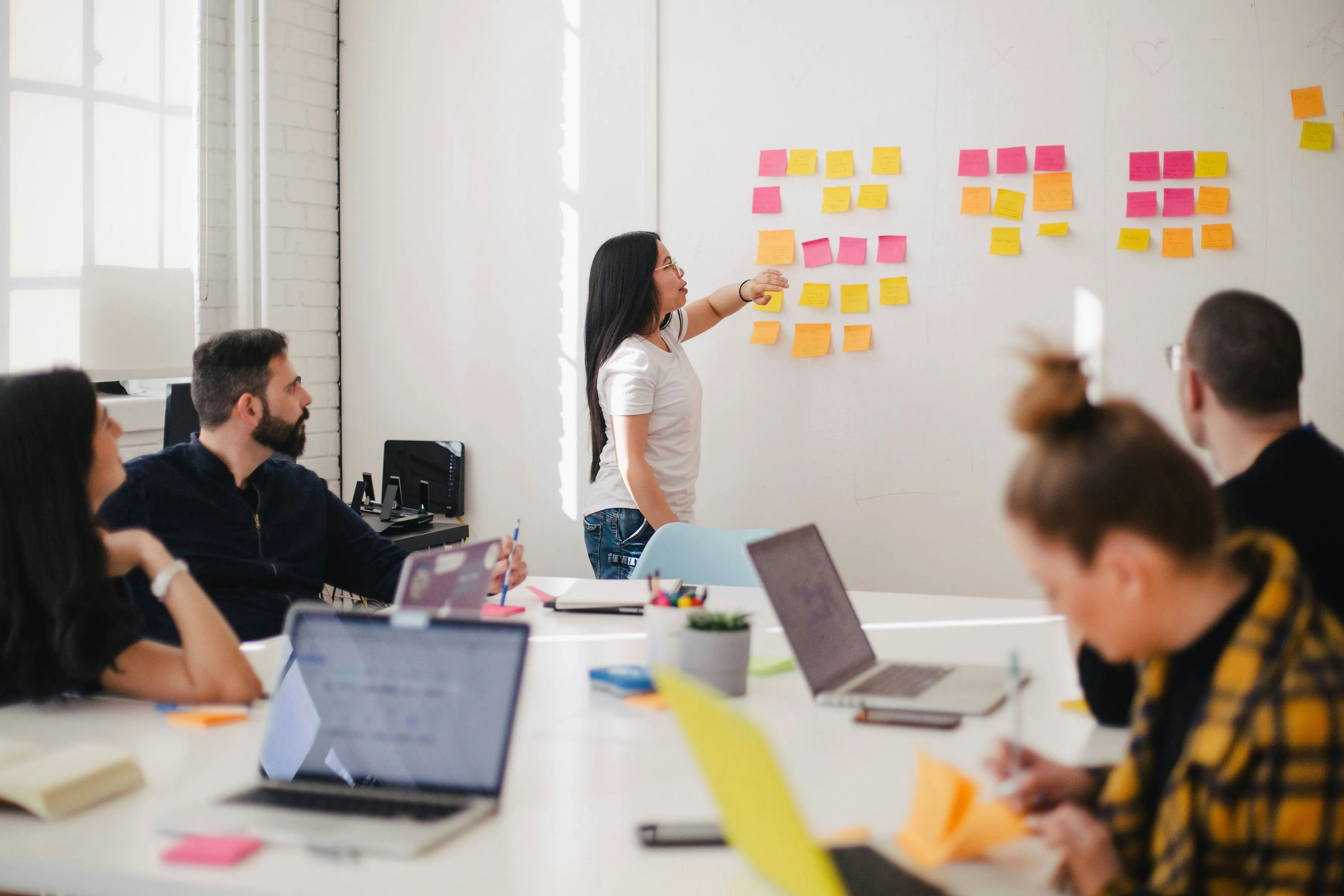
Indic clearly define and outline PCB assembly needs by specifying quality standards, production volume, costs, and customer/regulatory specifications.
We strategically source reliable components, considering quality, availability, and cost. Implement inventory management for timely availability.
We partner with a reputable facility to actively manufacture high-quality PCBs, specifying material, layering, and surface finish.
We select suitable equipment based on volume, complexity, and budget, such as soldering equipment and pick-and-place machines, inspection systems, and soldering irons for manual touch-up.
We develop a detailed process flow that outlines the sequence of operations for PCB assembly, including component placement, soldering, inspection, testing, and final packaging.
We create comprehensive work instructions and standard operating procedures (SOPs) for each step of the assembly process. These documents should provide clear guidance to operators on how to perform their tasks accurately and safely.
.jpg)
We actively train assembly operators and technicians on the assembly process, equipment operation, quality standards, and safety procedures. Implement a qualification program to ensure that personnel are competent to perform their assigned tasks.
We establish quality control measures and inspection criteria to monitor the quality of PCB assemblies throughout the manufacturing process. This may include visual inspection, automated optical inspection (AOI), X-ray inspection, and testing.
We continuously monitor and analyze key performance metrics such as defect rates, cycle times, and production yield to identify opportunities for process optimization and improvement. Implement corrective and preventive actions (CAPAs) to address root causes of defects and prevent recurrence.
We maintain comprehensive documentation of the assembly process, including production records, inspection reports, component traceability data, and any deviations or non-conformances encountered during production.
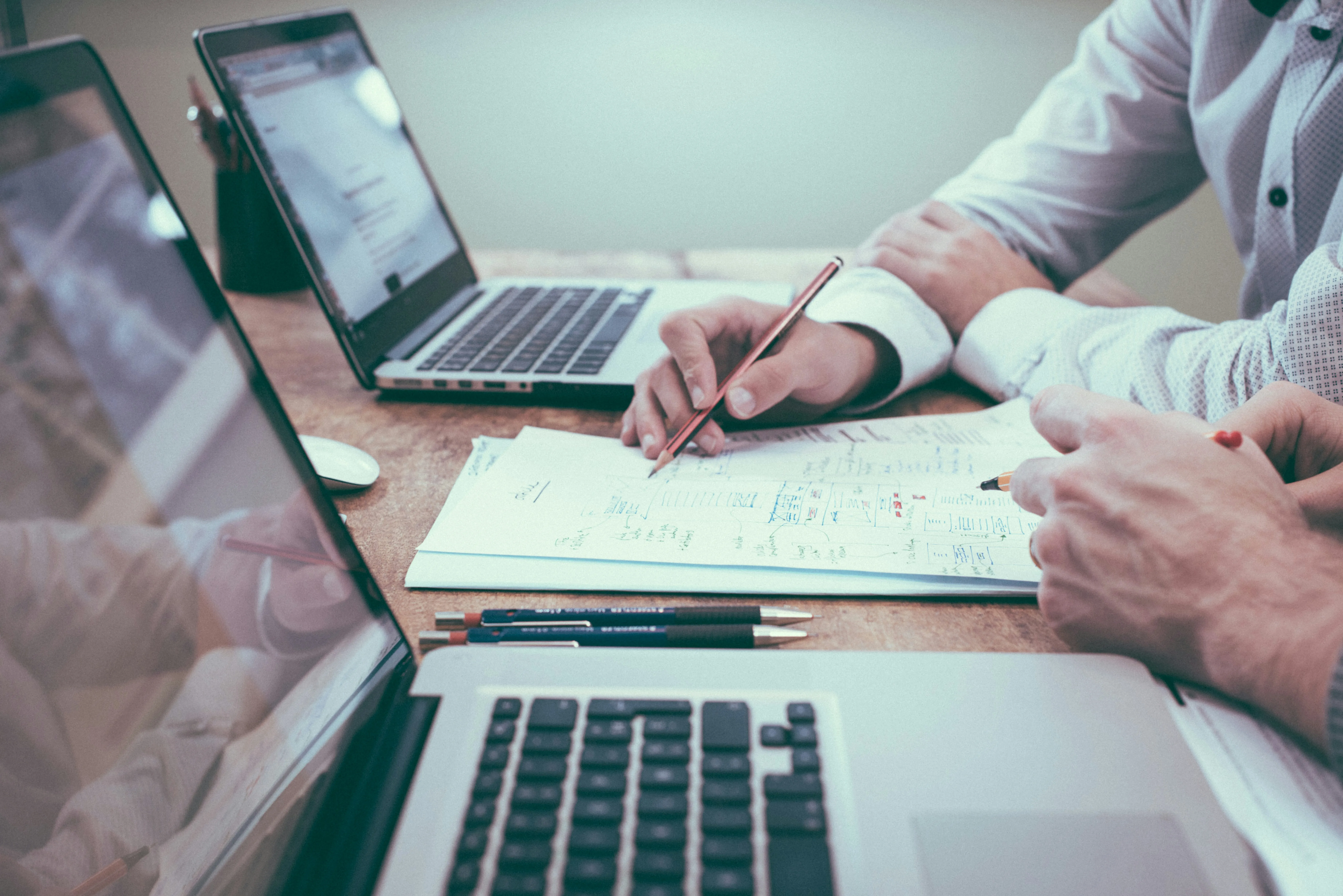
Our Capabilities
Design for Manufacturability (DFM): EMS providers work closely with original equipment manufacturers (OEMs) during the product design phase to ensure that the design can be efficiently manufactured. This involves analyzing the design for potential manufacturing issues, such as component placement, assembly complexity, and material selection, and making recommendations to improve manufacturability.
Prototyping and Pilot Production: EMS companies often engage in prototyping and pilot production runs to test and refine the manufacturing processes before full-scale production begins. This allows them to identify and address any issues early on, optimize production workflows, and ensure product quality and reliability.
Process Optimization: Process development in EMS focuses on optimizing each step of the manufacturing process to improve efficiency, reduce costs, and enhance product quality. This may involve refining equipment settings, streamlining assembly procedures, implementing automation where possible, and minimizing waste.
Supply Chain Management: Effective supply chain management is crucial for ensuring a steady flow of materials and components needed for production. Process development may involve working closely with suppliers to optimize inventory management, reduce lead times, and mitigate supply chain risks.
Quality Assurance and Testing: EMS providers implement rigorous quality assurance processes to ensure that products meet the highest standards of quality and reliability. This includes performing thorough testing and inspection throughout the manufacturing process, from incoming materials inspection to final product testing, and implementing corrective actions as needed to address any issues that arise.
Continuous Improvement: Process development in EMS is an ongoing effort that involves continuously monitoring and evaluating manufacturing processes to identify opportunities for improvement. This may include gathering feedback from employees, analyzing production data, and benchmarking performance against industry standards to identify areas for optimization.
Technology Adoption: EMS providers invest in the latest manufacturing technologies and equipment to improve efficiency, increase capacity, and enhance product quality. Process development may involve evaluating and adopting new technologies such as advanced robotics, additive manufacturing, and smart manufacturing systems to stay competitive in the industry.
Regulatory Compliance: EMS companies must adhere to various regulatory requirements and industry standards, such as ISO 9001, ISO 13485, and IPC standards, depending on the type of products they manufacture. Process development involves ensuring compliance with these standards through proper documentation, training, and quality management systems.
The 17 common steps include design, material selection, pattern transfer, etching, layer lamination, drilling, plating, solder mask application, silkscreen, surface finishing, testing, inspection, depaneling, packaging, and shipping. This comprehensive process ensures PCB reliability and performance.
The PCB Assembly (PCBA) process includes applying solder paste, placing components, soldering, inspection and testing. This ensures that all components are correctly mounted and the PCB functions as intended.
PCB fabrication involves transferring the circuit design onto a substrate, etching away excess material, drilling holes for components, and applying a protective solder mask. This process prepares the PCB for component assembly.
The developing process in PCB involves preparing the board for etching by applying a photosensitive material and then exposing it to light through a mask, defining the circuit pattern. This step is crucial for accurate circuitry layout on the PCB.
PCB assembly steps include solder paste printing, component placement, soldering (reflow or wave), inspection (AOI, X-ray, manual), and testing (functional, in-circuit). These ensure the correct assembly and functionality of PCBs. What is the production process of PCBs? The PCB production process encompasses design, material selection, patterning, etching, layer stacking, drilling, plating, solder mask application, and finishing. This multi-step process ensures high-quality and functional circuit boards.
The PCBA manufacturing process encompasses PCB fabrication, component procurement, assembly, testing, and quality assurance. It's a comprehensive approach from raw materials to a fully assembled, tested, and ready-to-use printed circuit board assembly.