Case Study: Resolving Flash Failure in Battery Management System PCBAs for an Automotive Company
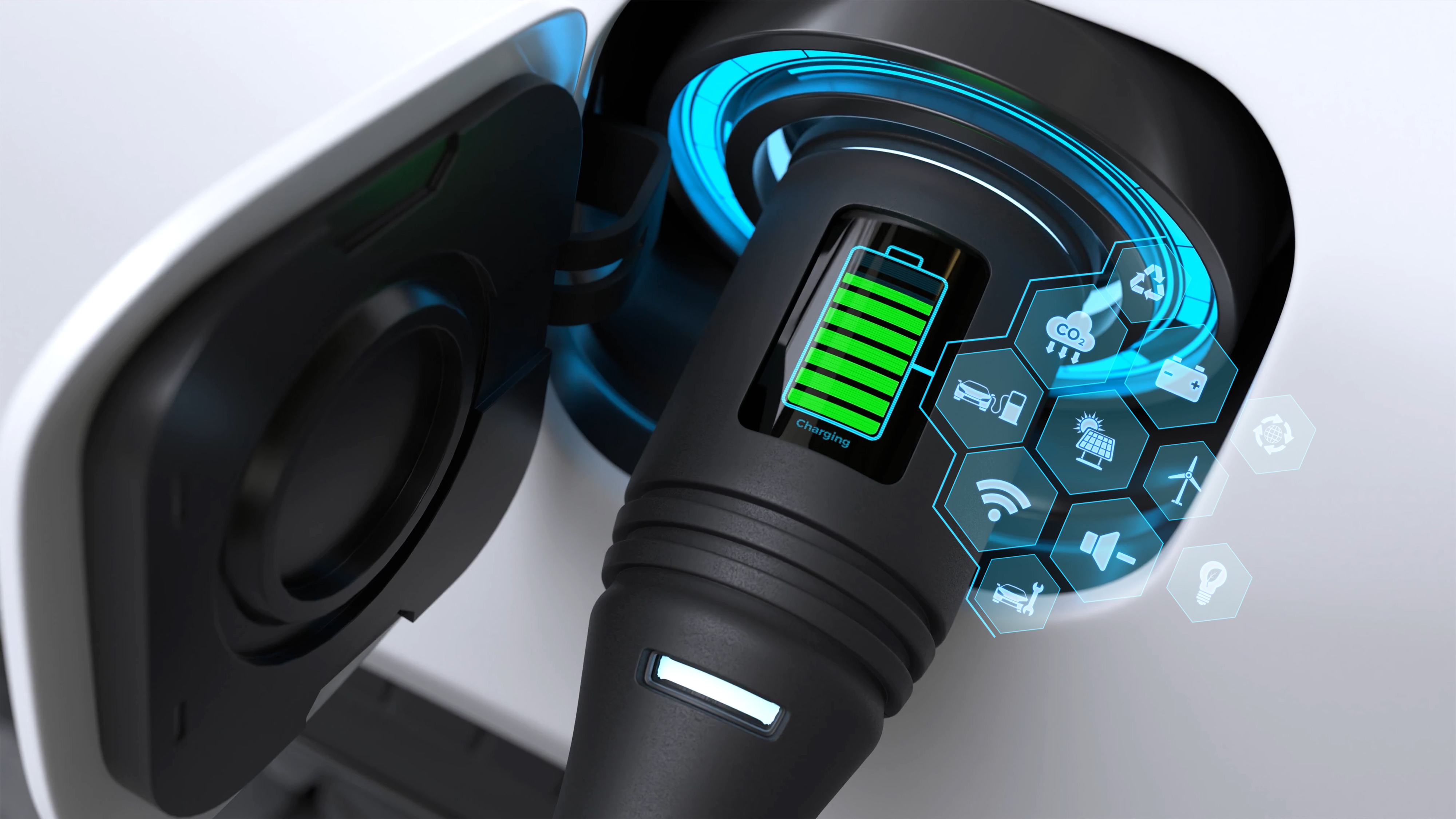
Overview
This case study examines a significant challenge encountered during the production of Printed Circuit Board Assemblies (PCBAs) for a Battery Management System (BMS) supplied to an automotive customer. A high failure rate due to flash memory issues in one particular IC component threatened production timelines and increased rework costs. Through collaborative problem-solving and software innovation, the issue was resolved, leading to substantial improvements in quality and efficiency.
Problem Statement
During testing, a high number of PCBAs failed due to a flash failure in that one particular IC. Customer quarantined the failed boards, which had accumulated since previous year. The failure was initially addressed to the IC supplier. However, the supplier's report indicated no issues with the IC itself. Further complicating the situation, customer was unable to share the IC code with the supplier for fault rectification, and the supplier declined to conduct further analysis without it.
Challenges
- The high number of failing PCBAs significantly impacted production yield and increased costs.
- The inability to access the IC code hindered effective troubleshooting by the supplier.
- The supplier's unwillingness to proceed without access to the code created a standstill.
- It was necessary to rule out any assembly process-related causes for the failures.
Analysis & Solution
To address the issue, the following actions were undertaken:
- High-level technical discussions were held between customer , the supplier, and the PCBA assembly team.
- Multiple trials were conducted with the tester vendor & production team , Design team to validate the assembly process, which successfully eliminated process-related causes suspected team.
- Software team developed a new software upgrade designed to fix the flash failure in that particular IC.
- The new software version was tested on the failed units. All units that passed the test after the upgrade were shipped to Customer.
Impact
- The implementation of the software upgrade led to a dramatic reduction in PPM from an average of 5000 PPM per production to 0 PPM.
- Resolution of the issue reduced the amount of space required for storing faulty boards.
- The new software version smoothed the testing process, ensuring efficiency and reliability.
- As of the case study's writing, no failures have been reported on units shipped after the software upgrade.
Conclusion
This case study demonstrates the successful resolution of acritical issue in Battery Management System PCBA production through collaborative effort and innovative software solutions. By addressing the flash failure in the IC, significant cost savings were realized, PPM levels were drastically reduced, and testing processes were streamlined.