PFMEA
Die Prozessausfallmodus- und -auswirkungsanalyse (PFMEA) ist eine strukturierte Methode zur Identifizierung und Priorisierung potenzieller Fehlerarten in einem Fertigungs- oder Montageprozess, zur Bewertung ihrer potenziellen Auswirkungen und zur Entwicklung von Minderungsstrategien zur Vermeidung oder Minimierung ihrer Auswirkungen.
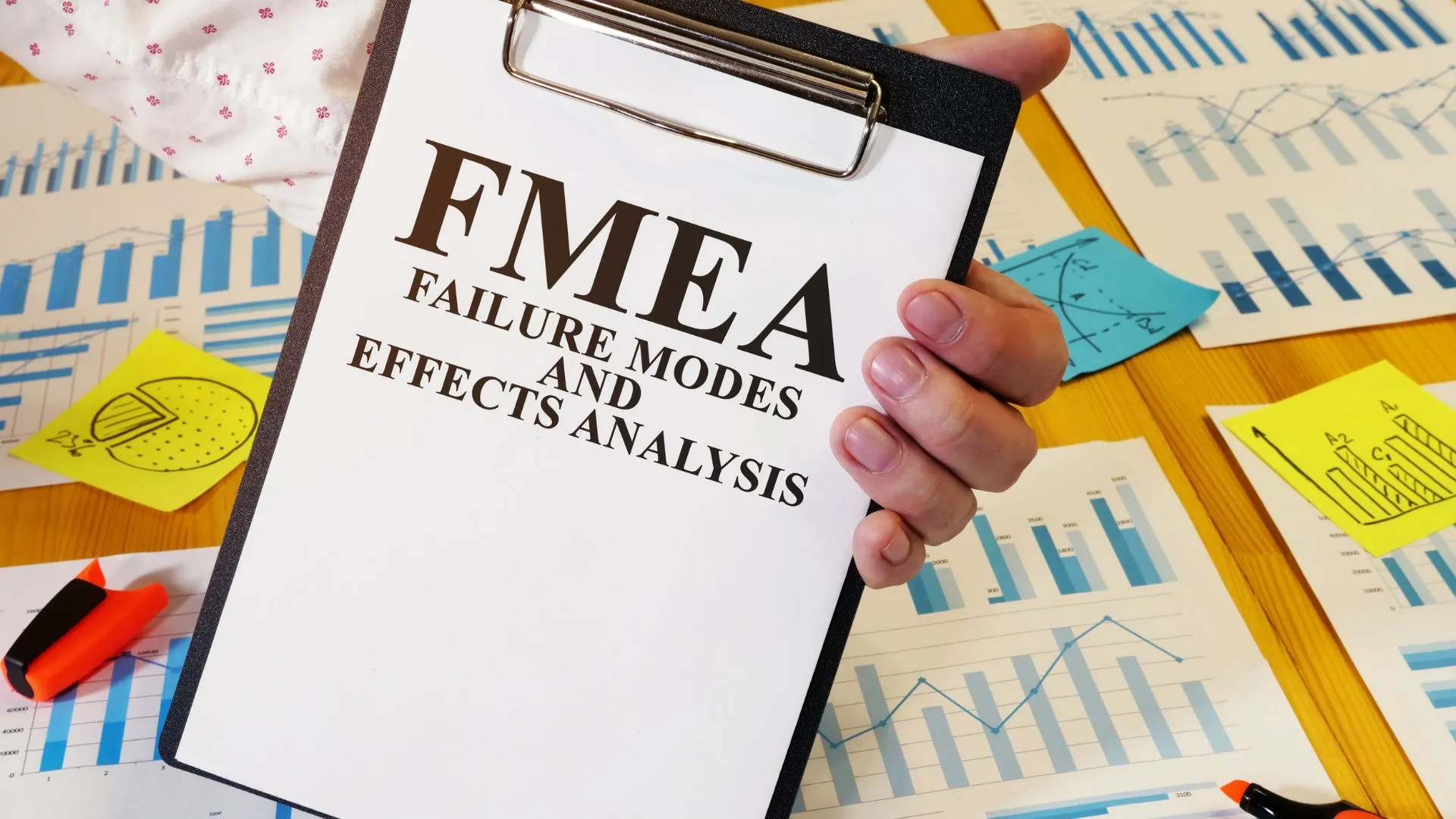
So führt Indic PFMEA aktiv durch:
Indic führt PFMEA aktiv durch, indem zunächst bestimmte Herstellungs- oder Montageprozesse wie Leiterplattenmontage, Spritzgießen, Bearbeiten oder Schweißen festgelegt werden. Anschließend wird ein funktionsübergreifendes Team zusammengestellt, das sich aus Prozessexperten und Vertretern der Qualitätssicherung, der Konstruktion, der Produktion und der relevanten Abteilungen zusammensetzt. Jeder Prozess wird sorgfältig in einzelne Schritte unterteilt, um eine umfassende Analyse potenzieller Fehlerursachen zu gewährleisten. In aktiven Brainstorming-Sitzungen untersucht Indic verschiedene Fehlerursachen und berücksichtigt dabei Faktoren wie Gerätestörungen, Bedienfehler, Materialfehler und Umgebungsbedingungen.
Indic bewertet die Auswirkungen der einzelnen Ausfallursachen auf Produktqualität, Sicherheit, Zuverlässigkeit, Kosten und Kundenzufriedenheit und ordnet den Schweregrad entsprechend auf einer numerischen Skala zu. Techniken zur Ursachenanalyse wie das 5-Warum-Diagramm oder das Fischgrätdiagramm werden verwendet, um die zugrunde liegenden Ursachen der Ausfallursachen zu ermitteln.
Die Bewertung der Wahrscheinlichkeit, mit der jeder Ausfallmodus auftritt und erkannt wird, ist für Indic ein proaktiver Schritt, der sich auf historische Daten, Erfahrungen und Expertenmeinungen stützt. Die Risk Priority Number (RPN) wird dann für jeden Ausfallmodus berechnet und dient als Grundlage für die Priorisierung der Maßnahmen zur Schadensbegrenzung. Indic priorisiert Ausfallarten mit hohem Risiko für Korrektur- und Präventionsmaßnahmen, zu denen Prozessanpassungen, Ausrüstungsverbesserungen oder Schulungsinitiativen gehören können.
Die kontinuierliche Überwachung und Überprüfung der umgesetzten Strategien gewährleistet deren kontinuierliche Wirksamkeit. Die PFMEA wird dynamisch aktualisiert, um Änderungen der Prozesse, Technologien oder Kundenanforderungen Rechnung zu tragen. Der proaktive PFMEA-Ansatz von Indic unterstreicht das Engagement von Indic für Qualität, Sicherheit und kontinuierliche Verbesserung der Fertigungsprozesse.
In unserem Bestreben, hochwertige elektronische Produkte zu liefern, integrieren wir PFMEA als proaktive Maßnahme in unsere Herstellungsprozesse. Unser Ansatz beinhaltet die Zusammenarbeit funktionsübergreifender Teams, darunter Ingenieure, Qualitätssicherungsspezialisten und Produktionsexperten.
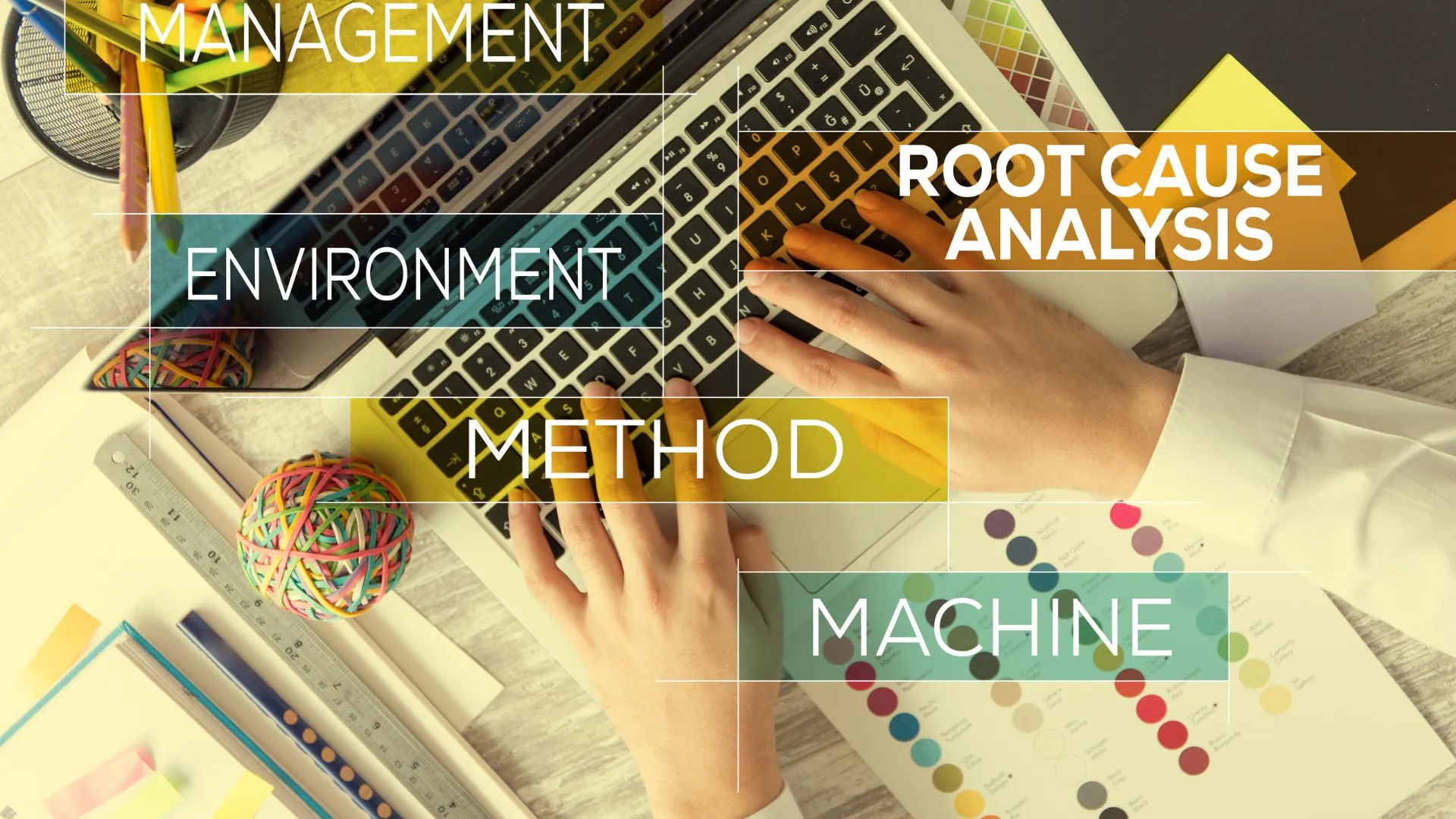
Unsere Fähigkeiten
- Risikobeurteilung
- Kritisches Denken
- Prozessverständnis
- Funktionsübergreifende Zusammenarbeit
- Datenanalyse
- Risikopriorisierung
- Ursachenanalyse
- Planung von Schadensbegrenzungen
- Umsetzung und Überwachung
- Dokumentation und Berichterstattung
- Einhaltung gesetzlicher Vorschriften
- Kontinuierliche Verbesserung
Yes, PFMEA (Process Failure Mode and Effects Analysis) is a proactive quality tool used in the manufacturing industry to identify and mitigate potential failures in a process before they occur, enhancing product quality and reliability.
PFMEA, or Process Failure Mode and Effects Analysis, is a structured approach to identify, prioritize, and mitigate risks in a manufacturing process, aiming to improve quality and reliability by preventing process-related failures.
The three types of FMEA are Design FMEA (DFMEA), which focuses on potential failures in product design; Process FMEA (PFMEA), which identifies potential failures in manufacturing processes; and System FMEA (SFMEA), which analyzes failures at the system or subsystem level.
Using a PFMEA involves mapping out each step of the manufacturing process, identifying potential failure modes, assessing their impact and likelihood, prioritizing them based on risk, and implementing control measures to mitigate or eliminate these risks.
An early PFMEA is important because it allows for the identification and mitigation of potential process failures before they become costly or dangerous, leading to a more efficient, reliable, and safe manufacturing process.
PFMEA (Process Failure Mode and Effects Analysis) is a systematic analytical tool used to identify and address potential failures in a manufacturing or assembly process. It's used by creating a step-by-step analysis for each process component, identifying potential failure modes, assessing their impact, and implementing mitigation strategies.
PFMEA (Process FMEA) focuses specifically on identifying and reducing risks in manufacturing processes, while FMEA is a broader term that can refer to Design FMEA (DFMEA), Process FMEA (PFMEA), or System FMEA (SFMEA), each targeting different aspects of product and process reliability.
Design FMEA (DFMEA) focuses on potential design-related failures and their effects on product performance, while Process FMEA (PFMEA) targets potential failures in the manufacturing process and their impact on product quality.
The main types of FMEAs are Design FMEA (DFMEA), Process FMEA (PFMEA), and System FMEA (SFMEA), each analyzing risks at different stages of product development and manufacturing to enhance reliability and safety.
An example of PFMEA in manufacturing could involve the assembly line for electronic devices, where PFMEA helps identify potential issues like incorrect component placement or soldering defects, allowing for preventive measures to be implemented.