Probleme mit der Lötbarkeit
Identifizieren und beseitigen Sie anfällige Bereiche, in denen zu wenig Lötmaterial, Lötspritzer, Lötkurzschlüsse oder nicht robuste Lötstellen für den SMT- und PTH-Prozess vorhanden sind
Indic bekämpft proaktiv Lötbarkeitsprobleme bei SMT- und PTH-Prozessen. Unser DFM-Review identifiziert potenzielle Probleme frühzeitig. Dazu gehören auch die Analyse von Faktoren wie Größe und Form der Bremsbeläge, Platzierung der Komponenten und Wärmeprofile. Wir verwenden hochwertige Materialien, fortschrittliche Ausrüstung und strenge Inspektionen während des gesamten Prozesses. Durch kontinuierliche Verbesserung minimieren wir Fehler, verbessern die Produktqualität und stellen die Produktionseffizienz sicher. Entscheiden Sie sich für Indic, wenn Sie zuverlässige Lötlösungen und ein beruhigendes Gefühl erwarten.
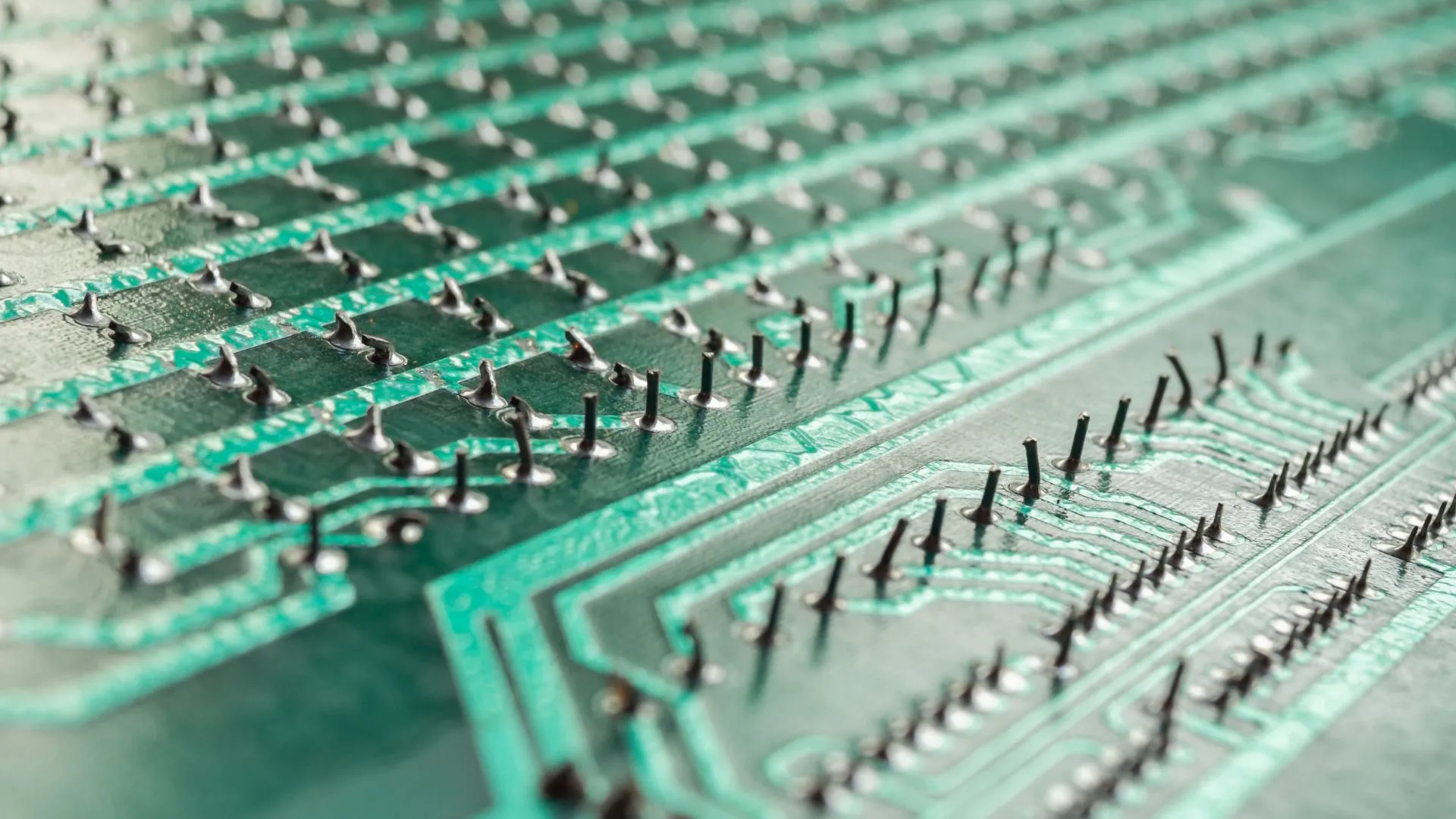
Bei Indic zeichnen wir uns durch die Identifizierung und Beseitigung potenzieller Lötbarkeitsprobleme bei SMT- (Surface Mount Technology) und Platated Through-Hole (PTH) -Prozessen aus. Unser proaktiver Ansatz beginnt mit einer gründlichen Prüfung des Designs for Manufacturability (DFM), bei der wir Faktoren wie die Größe und Form der Polster, die Platzierung der Komponenten und die thermischen Profile analysieren, um vorhersehbare Probleme frühzeitig zu beheben. Wir legen bei jedem Schritt großen Wert auf Qualität und verwenden hochwertige Materialien, modernste Ausrüstung und strenge Inspektionsverfahren während des gesamten Lötprozesses. Mit unseren kontinuierlichen Verbesserungsbemühungen minimieren wir Fehler, verbessern die Produktqualität und stellen die Produktionseffizienz sicher, sodass Sie sich keine Sorgen machen müssen.
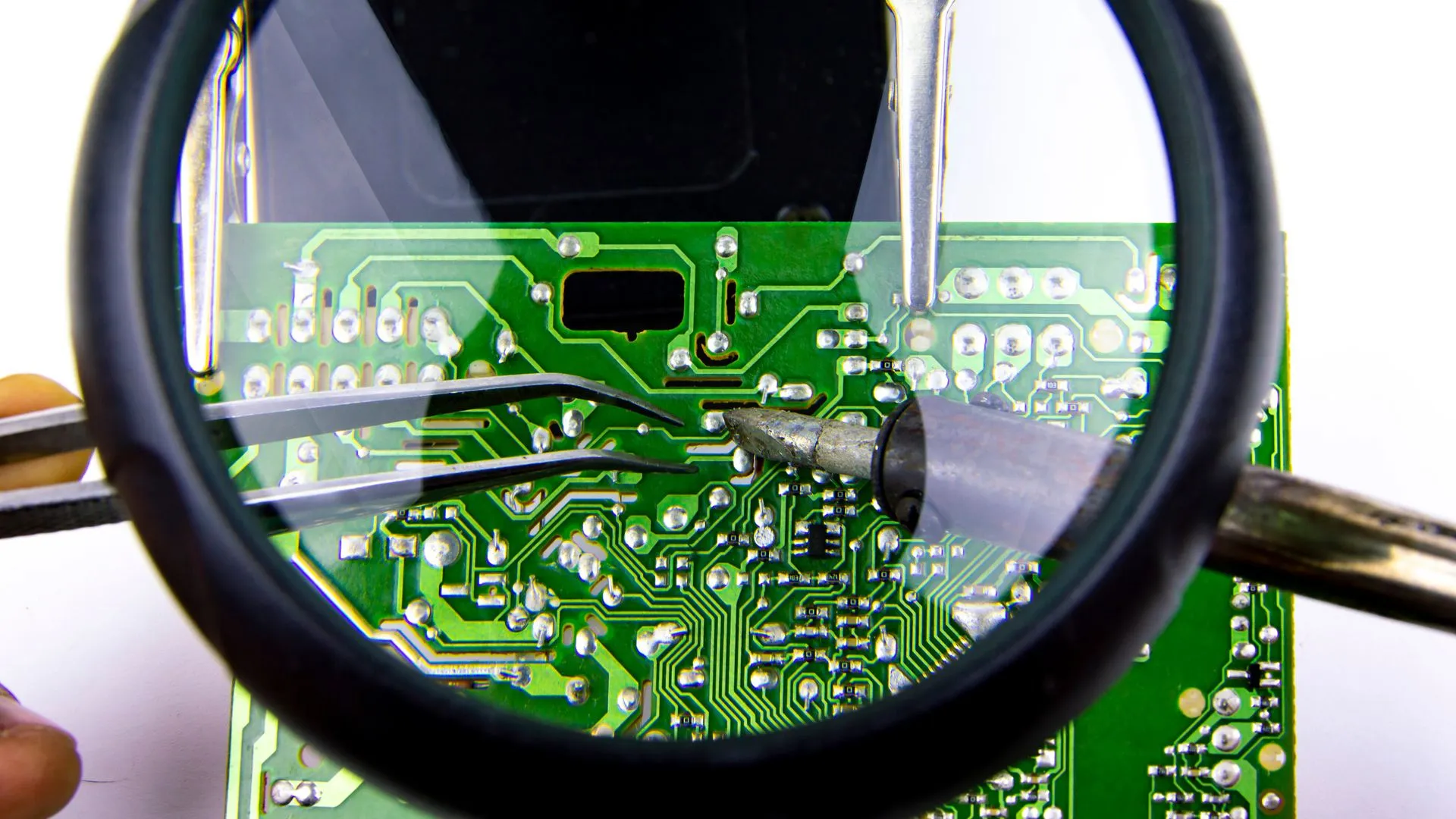
- SMT-Löten
- Wellenlöten
- Automatisches Löten
- Selektives Löten
- Manuelles Löten
- Röntgeninspektion
- 100-facher Umfang von der Inspektion bis zur Fehlervalidierung
Soldering defects are imperfections in solder joints that can lead to failures in electrical circuits. They include cold solder joints, solder bridges, insufficient or excessive solder, tombstoning, and voids.
Avoid common PCB soldering problems by ensuring proper PCB and component storage to prevent oxidation, using suitable flux and solder, maintaining optimal soldering temperatures, and employing adequate preheating and cleaning processes.
Solderability refers to the ability of a material, typically a metal, to be soldered effectively, allowing for proper wetting and adhesion of the solder to the material's surface.
Common soldering problems include cold joints, overheated components, solder bridges (shorts), insufficient wetting, and excessive flux residue. These issues can compromise electrical connections and the reliability of the PCB.
A PCB solderability test evaluates a board's ability to be soldered to, ensuring that the solder properly wets and adheres to the component leads and pads. This test is crucial for assessing the quality of PCB materials and surface finishes.
Major soldering defects include cold joints, dry joints, solder bridges, tombstoning, solder balls, and voids, each affecting the functionality and reliability of the PCB.
Cold/Dry Joints: Reheat the joint with proper solder and flux. Solder Bridges: Remove excess solder with desoldering braid. Solder Balls: Clean the area and reapply solder with correct temperature. Tombstoning: Adjust component placement and reflow solder. Voids: Apply additional flux and reheat to allow solder to fill gaps.
To avoid bad solder joints, ensure clean and well-prepared surfaces, use the correct solder and flux, apply appropriate heat, and adhere to optimal soldering times. Proper technique and equipment maintenance are also crucial.
The issue with solder wetting occurs when the solder fails to spread on the metal surface being soldered, leading to weak or unreliable joints. Poor wetting can result from oxidation, contamination, or inadequate flux.