INDIC leistet Pionierarbeit beim schnellen 4-tägigen Montagezyklus von Ladegeräten für Elektrofahrzeuge
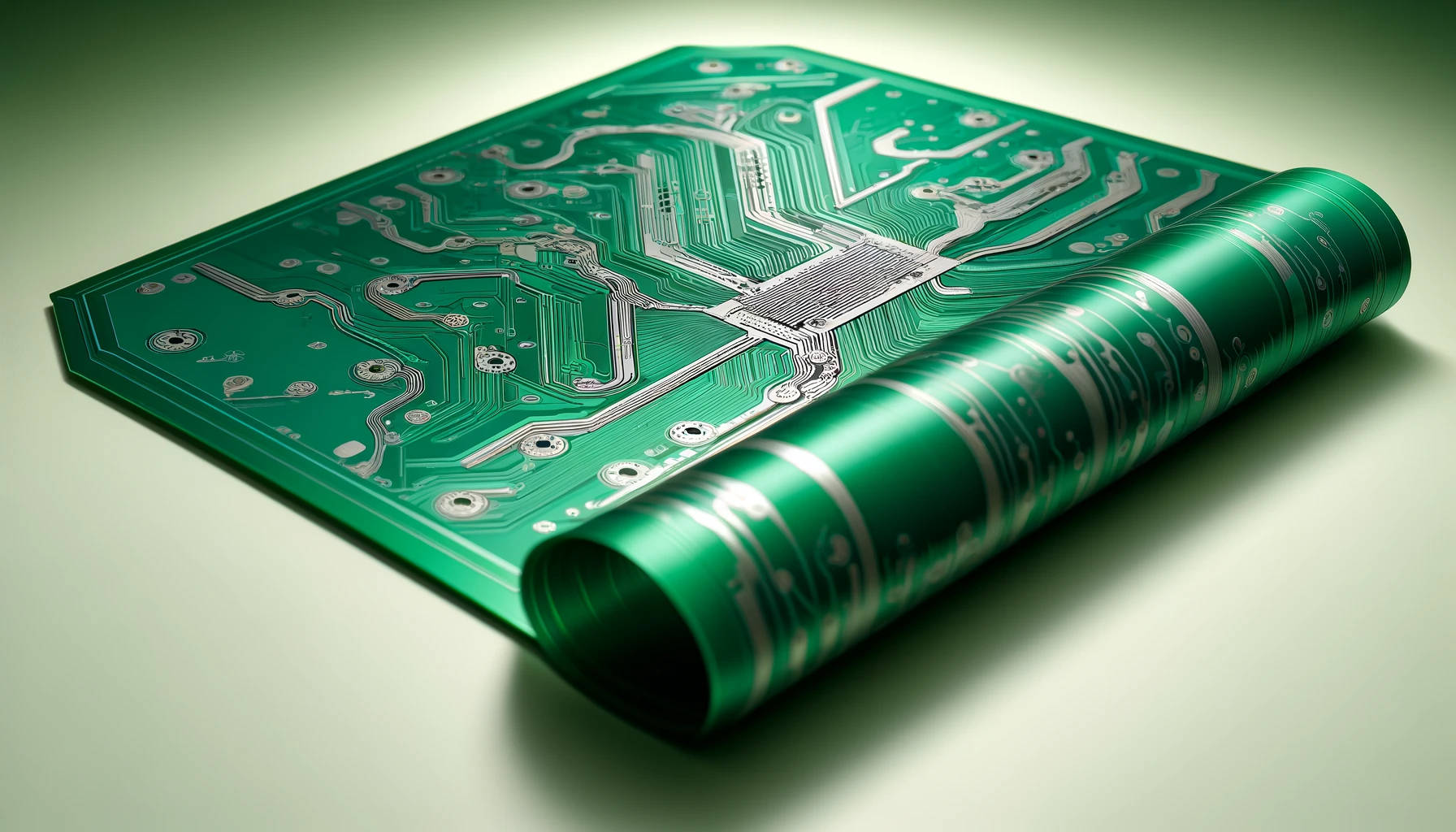
In der sich schnell entwickelnden Elektrofahrzeugbranche (EV) spielen die Entwicklung und Zertifizierung von Ladegeräten eine entscheidende Rolle bei der Aufrechterhaltung der Sicherheitsstandards und der Gewährleistung der Kompatibilität mit der Ladeinfrastruktur. Ein führendes Automobilunternehmen auf dem Markt für Elektrofahrzeuge zielte darauf ab, die Produktion eines Baugruppe 3-Rad-Ladegerät für ihre Elektrofahrzeuge, die von der Abhängigkeit von internationalen Lieferanten zur inländischen Produktion übergehen. Diese Fallstudie untersucht die Herausforderungen und innovativen Lösungen, die mit der Erlangung der Zertifizierung durch die Automotive Research Association of India (ARAI) für diese wichtige Komponente verbunden sind.
Die Herausforderung
Das Projekt stand vor einer erheblichen Hürde: Der bestehende Prozess zur Montage des Ladegeräts dauerte zwei Wochen vom Rohmaterial bis zur fertigen Ware. Für die Beantragung der ARAI-Zertifizierung — ein entscheidender Schritt zur Überprüfung der Sicherheit und Leistung des Ladegeräts — benötigte das Unternehmen jedoch innerhalb von nur fünf Tagen mindestens 10 Geräte. Dieser enge Zeitplan stellte angesichts des komplizierten Prozesses der Montage von PFC-Platinen (Power Factor Correction), Steuerplatinen, Stromversorgungsplatinen und der Endmontage der Box eine große Herausforderung dar.
Die innovative Lösung
Als Antwort auf diese Herausforderung entwickelte Indic, der Hersteller, der mit der Herstellung der Ladegeräte beauftragt war, einen überarbeiteten Plan, um die Produktion zu beschleunigen, ohne die Qualität zu beeinträchtigen. Zu den wichtigsten Innovationen gehörten:
- Parallele Verarbeitung: Durch die gleichzeitige Arbeit an der PFC-Platine und das Laden von SMT-Komponenten auf der Ober- und Unterseite sowie die Priorisierung der Montage der Leistungsplatine aufgrund ihrer kritischen Natur konnte Indic die Produktionszeit erheblich verkürzen.
- Priorisierung der Box Build Assembly: Da mit der Integration des Box-Builds begonnen wurde, bevor die Platinen fertig waren, konnten die Montage des Außengehäuses und der Vergussprozess parallel zur Leiterplattenproduktion abgeschlossen werden.
- Effiziente Integration: Durch die Integration der Eingangs- und Ausgangsstromversorgungskabel in die Box-Build-Lösung wurde der Prozess weiter optimiert und sichergestellt, dass alle Komponenten effizient und effektiv zusammengebaut wurden.
Auswirkung
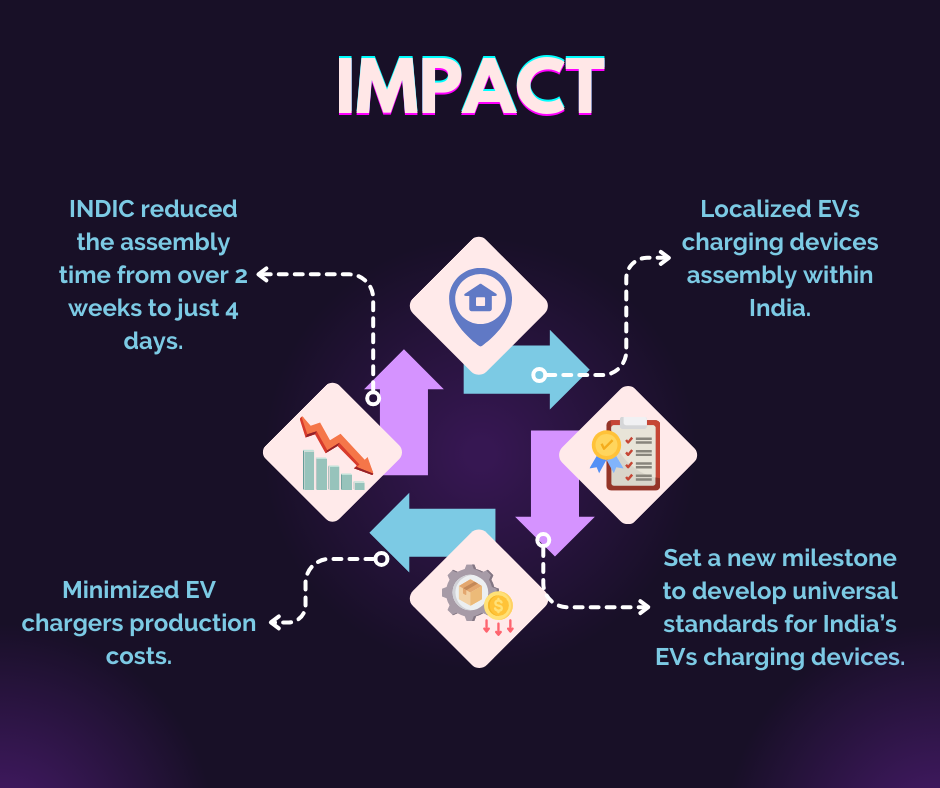
INDIC hat erfolgreich ein hochfunktionales Modell entwickelt, das die Montage und das Testen kompletter Ladegeräte für Elektrofahrzeuge auf nur noch wenige Schritte vereinfachte vier Tage, mit Lieferungen an das EV-Unternehmen am fünften Tag. Dadurch wurde die Zykluszeit der Montage erheblich reduziert. Zuvor waren es mindestens zwei Wochen zur Herstellung eines 3-kW-EV-Ladegeräts.
INDIC nutzte seine robuste Produktions- und Montageinfrastruktur für elektronische Komponenten, die über einen langjährigen Betrieb aufgebaut wurde, und erreichte vollständige Lokalisierung seiner Herstellung von EV-Ladegeräten. Alle Geräteteile und Montageprozesse werden vollständig in den lokalen Einrichtungen von INDIC abgewickelt, was eine erhebliche Rückgang der Produktionskosten durch Nutzung lokaler Komponentenlieferungen und Fertigungskapazitäten.
Darüber hinaus war das Fehlen einheitlicher Standards unter den Herstellern von Elektrofahrzeugen in Indien und weltweit ein erhebliches Hindernis für die Marktentwicklung. Diese Initiative von INDIC stellt einen entscheidenden Schritt nach vorne dar und markiert einen neuen Meilenstein in den gemeinsamen Bemühungen zur Einführung universeller Standards in diesem Bereich.
Über die Montage von Indic- und EV-Ladegeräten in Indien
Der Erfolg von Indic bei diesem Projekt ist ein wichtiger Meilenstein bei der Lokalisierung der Produktion von Elektrofahrzeug-Ladegeräten in Indien. Zuvor war der Markt stark von Importen aus China abhängig, aber geopolitische Spannungen und das Streben nach Eigenständigkeit haben die Bemühungen zum Ausbau der inländischen Kapazitäten beflügelt. Indics Erfolg bei der Herstellung und Zertifizierung von Ladegeräten im Inland verdeutlicht das Potenzial Indiens, eine führende Position bei der Entwicklung der Infrastruktur für Elektrofahrzeuge einzunehmen.
Fazit
Diese Fallstudie beleuchtet die innovativen Ansätze und die strategische Planung, die erforderlich sind, um die Herausforderungen der Fertigung in der schnelllebigen Elektrofahrzeugbranche zu bewältigen. Die Fähigkeit von Indic, die engen Fristen für die ARAI-Zertifizierung einzuhalten, unterstützte nicht nur die Ziele des EV-Herstellers, die Produktion zu lokalisieren, sondern setzte auch neue Maßstäbe für Effizienz und Wirtschaftlichkeit bei der Herstellung von Ladegeräten. Da der Markt für Elektrofahrzeuge weiter wächst, werden solche Erfolge entscheidend für den Aufbau robuster, lokaler Lieferketten sein, die die Nachfrage nach nachhaltigen Transportlösungen decken können.