PFMEA
プロセス故障モードおよび影響分析(PFMEA)は、製造または組立プロセスにおける潜在的な故障モードを特定して優先順位を付け、その潜在的な影響を評価し、その影響を防止または最小限に抑えるための緩和戦略を開発するために使用される構造化された方法です。
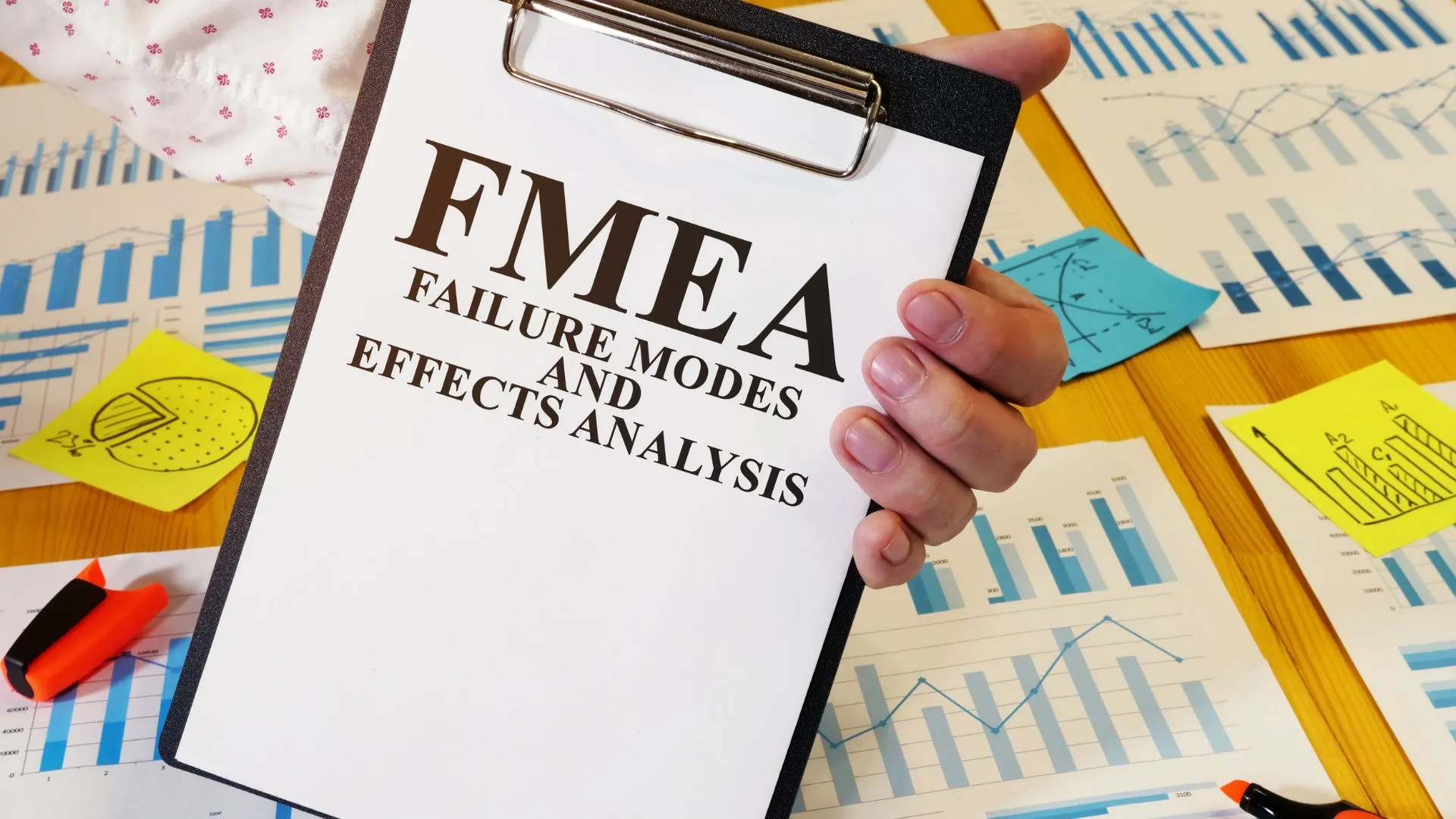
インドがPFMEAを積極的に実施している方法は次のとおりです。
Indcは、まずPCBアセンブリ、射出成形、機械加工、溶接などの特定の製造または組立プロセスを特定することにより、PFMEAを積極的に実施しています。次に、プロセスの専門家と、品質保証、エンジニアリング、生産、および関連部門の代表者で構成される、機能横断的なチームが結成されます。潜在的な故障モードを包括的に分析できるように、各プロセスは個々のステップに細心の注意を払って分割されます。インディックは活発なブレインストーミングセッションを通じて、機器の誤動作、オペレーターのミス、材料の欠陥、環境条件などの要因を考慮して、さまざまな故障モードを探ります。
Indcは、各故障モードが製品の品質、安全性、信頼性、コスト、および顧客満足度に及ぼす影響を評価し、それに応じて数値スケールで重大度評価を割り当てます。5 つの理由やフィッシュボーン図などの根本原因分析手法を使用して、故障モードの根本的な原因を特定します。
過去のデータ、経験、専門家の判断に基づいて、各故障モードが発生して検出される可能性を評価することは、インド人にとって積極的なステップです。次に、各故障モードのリスク優先度番号 (RPN) が計算され、軽減努力の優先順位付けの指針となります。Indecは、是正措置や予防措置として、リスクの高い故障モードを優先しています。これには、プロセスの調整、機器のアップグレード、またはトレーニングの取り組みが含まれる場合があります。
実施された戦略の継続的な監視とレビューにより、その継続的な有効性が確保されます。PFMEAは、プロセス、テクノロジー、または顧客要件の変化を反映して動的に更新されます。インドの PFMEA への積極的なアプローチは、品質、安全性、製造プロセスの継続的な改善への取り組みを明確に示しています。
高品質の電子製品を提供することへの取り組みの一環として、積極的な対策としてPFMEAを製造プロセスに統合しています。当社のアプローチでは、エンジニア、品質保証専門家、製造専門家など、部門を超えたチームが協力して取り組んでいます。
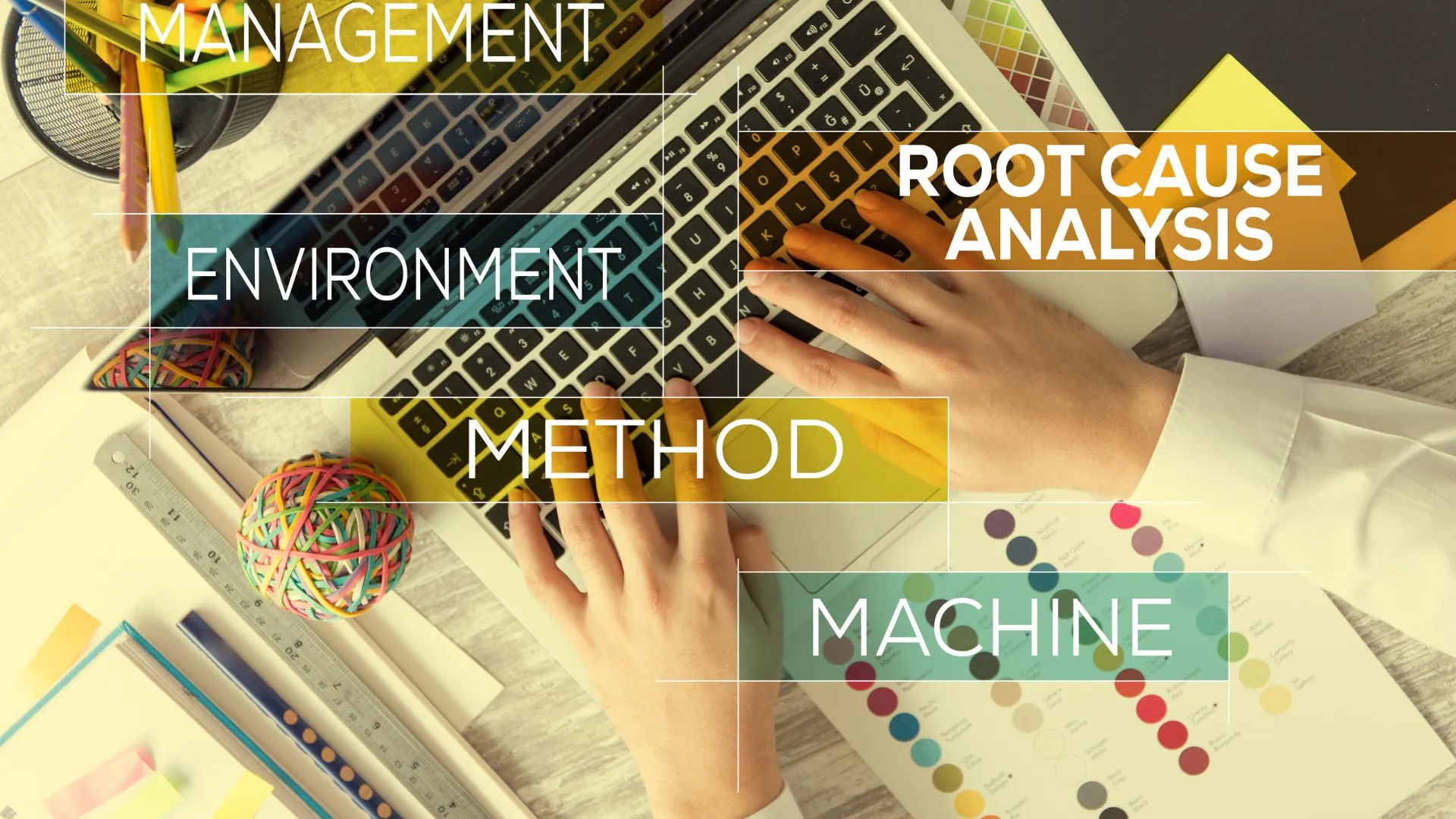
私たちの能力
- リスクアセスメント
- クリティカル・シンキング
- プロセス理解
- 部門間のコラボレーション
- データ分析
- リスクの優先順位付け
- 根本原因分析
- 緩和計画
- 実装と監視
- ドキュメンテーションとレポート
- 規制コンプライアンス
- 継続的改善
Yes, PFMEA (Process Failure Mode and Effects Analysis) is a proactive quality tool used in the manufacturing industry to identify and mitigate potential failures in a process before they occur, enhancing product quality and reliability.
PFMEA, or Process Failure Mode and Effects Analysis, is a structured approach to identify, prioritize, and mitigate risks in a manufacturing process, aiming to improve quality and reliability by preventing process-related failures.
The three types of FMEA are Design FMEA (DFMEA), which focuses on potential failures in product design; Process FMEA (PFMEA), which identifies potential failures in manufacturing processes; and System FMEA (SFMEA), which analyzes failures at the system or subsystem level.
Using a PFMEA involves mapping out each step of the manufacturing process, identifying potential failure modes, assessing their impact and likelihood, prioritizing them based on risk, and implementing control measures to mitigate or eliminate these risks.
An early PFMEA is important because it allows for the identification and mitigation of potential process failures before they become costly or dangerous, leading to a more efficient, reliable, and safe manufacturing process.
PFMEA (Process Failure Mode and Effects Analysis) is a systematic analytical tool used to identify and address potential failures in a manufacturing or assembly process. It's used by creating a step-by-step analysis for each process component, identifying potential failure modes, assessing their impact, and implementing mitigation strategies.
PFMEA (Process FMEA) focuses specifically on identifying and reducing risks in manufacturing processes, while FMEA is a broader term that can refer to Design FMEA (DFMEA), Process FMEA (PFMEA), or System FMEA (SFMEA), each targeting different aspects of product and process reliability.
Design FMEA (DFMEA) focuses on potential design-related failures and their effects on product performance, while Process FMEA (PFMEA) targets potential failures in the manufacturing process and their impact on product quality.
The main types of FMEAs are Design FMEA (DFMEA), Process FMEA (PFMEA), and System FMEA (SFMEA), each analyzing risks at different stages of product development and manufacturing to enhance reliability and safety.
An example of PFMEA in manufacturing could involve the assembly line for electronic devices, where PFMEA helps identify potential issues like incorrect component placement or soldering defects, allowing for preventive measures to be implemented.